plastic finishing solutions
Discover the machine for finishing required for plastic products
Go to products
What is meant by the industrial surface finishing of plastic substrates?
To start with, there are many different materials that are classified as plastic, from thermoplastic polymers such as polypropylene (PP), polycarbonate (PC), polyethylene (PET), ABS and PVC to PMMA and these can be found in moulded or extruded form and used for several products. According to size, shape, production volumes and what they are used for, plastic elements can be finished using different industrial processes. Spray coating, wrapping, industrial digital printing, as well as drying and curing are a few examples of the finishing processes they may undergo.
Why is plastic finishing so important in key industrial sectors?
In people’s minds, plastic is a cheap material, often associated with disposable items. Where it is used for furniture or in the construction industry or the automotive sector, the finishing process has, among others, the aim of embellishing the plastic elements to make them attractive and enhance their perceived value. There are different ways to decorate plastic substrates and even ways to customise the end product. These processes include:

Wrapping

Coating

Excimer matting

Industrial digital printing
In which industries are plastic finishing solutions used?
Application fields
Here is a selection of plastic finished specific products
APPLICATIONS

Panels

Interior components

Chairs

Plastic components
Focus On
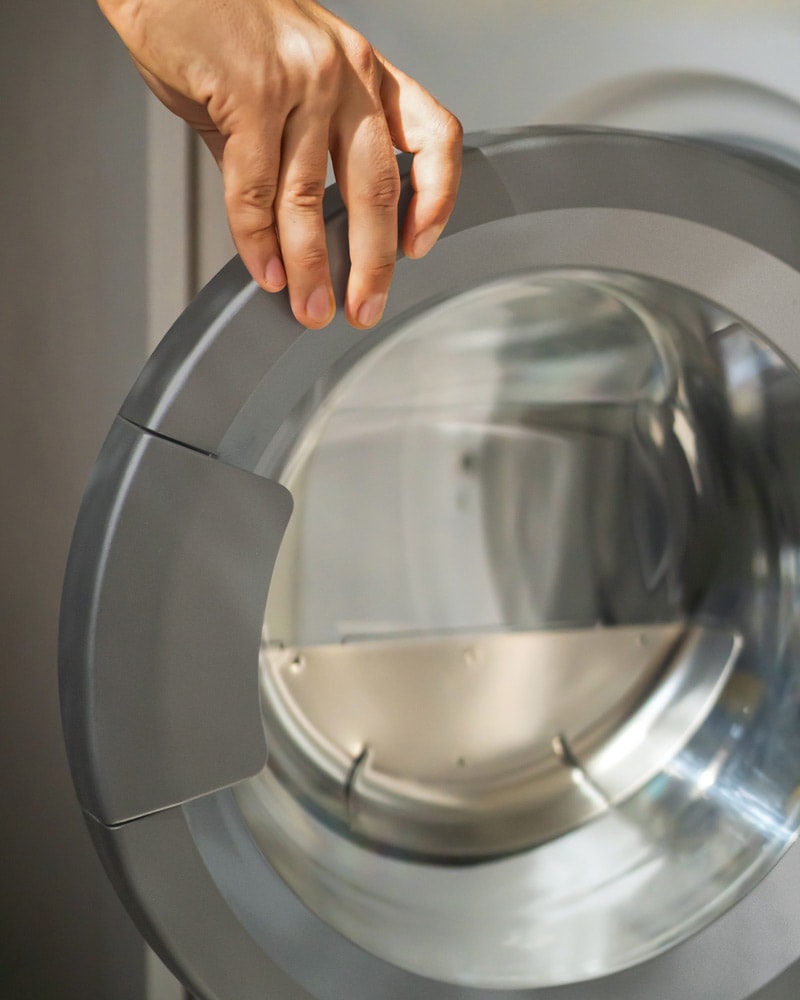
Excimer matting
Plastic panels can be given a deep matt finish using excimer matting technology as a sustainable solution featuring exclusive patents which reduce nitrogen consumption and relative costs.
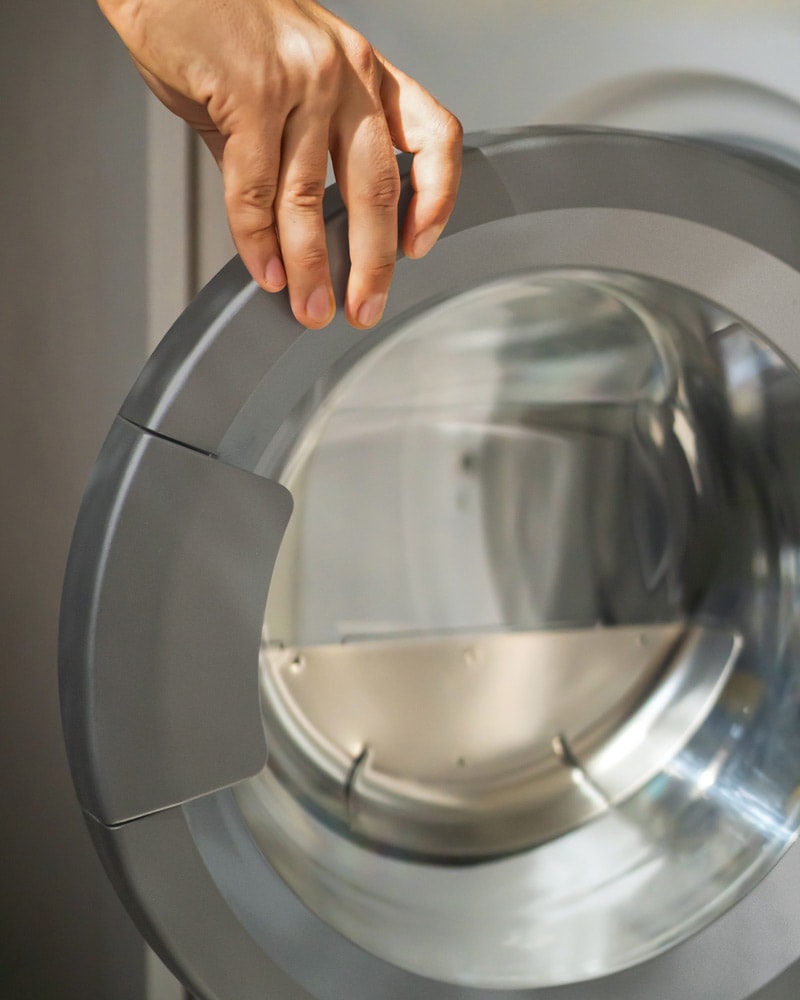
Technologies for plastic material processing and finishing
Plastic finishing is quite varied and the technologies used to complete the process are different according to the product or the desired effect. These are a selection of the most common technologies:
For excellent transfer efficiency, this coating technique can be used on flat panels and panels with shallow grooves, performed on specially equipped roller coaters. For ultra-high-gloss surface finishing, a Laser roller is the perfect solution.
Discover moreA flexible solution which ensures coating consistency applying lacquer to all sides of a 3D product. Spray coating is accomplished on flatbed lines or overhead lines with special spraying robots.
Discover moreThe ideal solution for customisation or batch one requirements, this technology transforms a unique digital image into a printed decoration and can be integrated into lines using other coating technologies.
Discover morePart of automatic equipment providing solutions for a complete process including an adhesive coater unit, wrapping is performed on profiles and window frames in PVC.
Discover moreDifferent ovens implementing IR or UV technologies are available to dry the lacquers used to coat the plastic substrate.
Discover moreThin sheets
What special finishing technologies can be used for thin PMMA sheets?
Specially adapted roller coating equipment that handles thin plastic sheets is a consolidated solution which we configure to suit your requirement.
Firstly, coating must be performed in a controlled environment, pressurised to avoid contamination from dust, and special pumps are fitted to the coating equipment to eliminate the risk of air bubbles, the two most common defects of a coated PMMA sheet.
To keep the substrate rigid during coating, an upper application roller works in unison with a lower support roller that features a cleaning device to keep the bottom side of the sheet free from lacquer.
Fibrous plastic sheets for gaskets can also be coated in a similar way, involving a simpler and equally effective process.
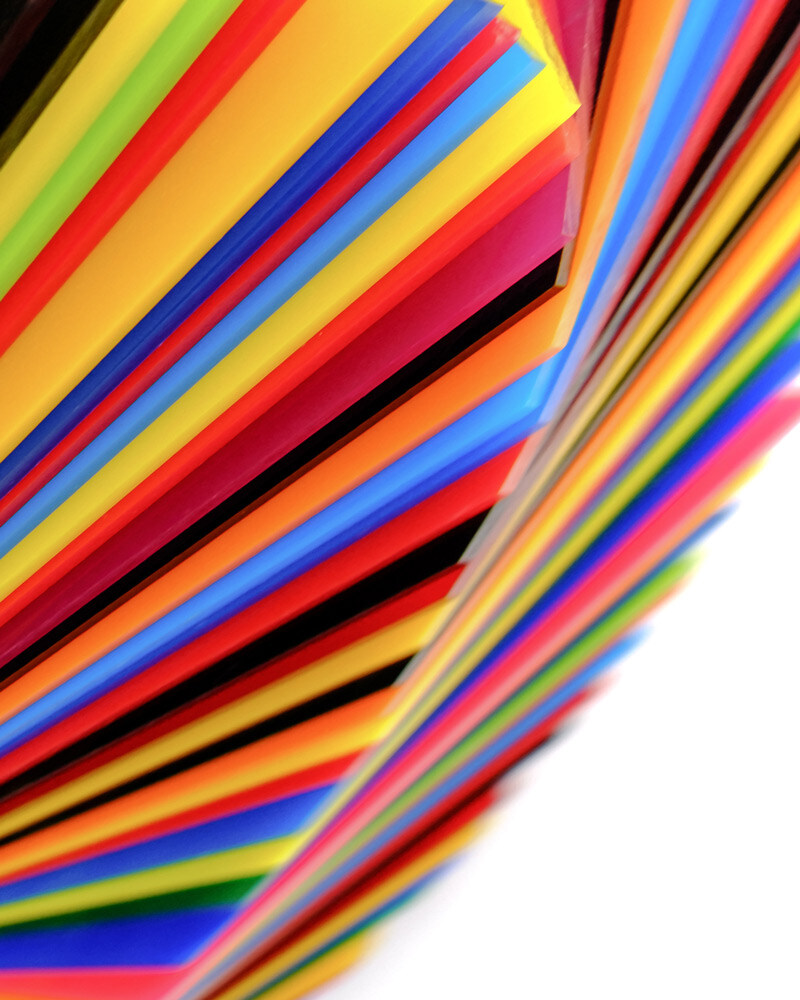
Discover the machines for industrial finishing of plastics
Machines
Case studies
Case study
WHITEPAPER
Industrial digital printing has unlimited potential
Discover all the potential effects that you can obtain on different substrates thanks to digital printing.
Downoload the White Paper
Learn More
MAGAZINE
We’ve been innovating in the surface finish field for sixty years.
Tell us where you want to go and our finishing experts will help you get there.
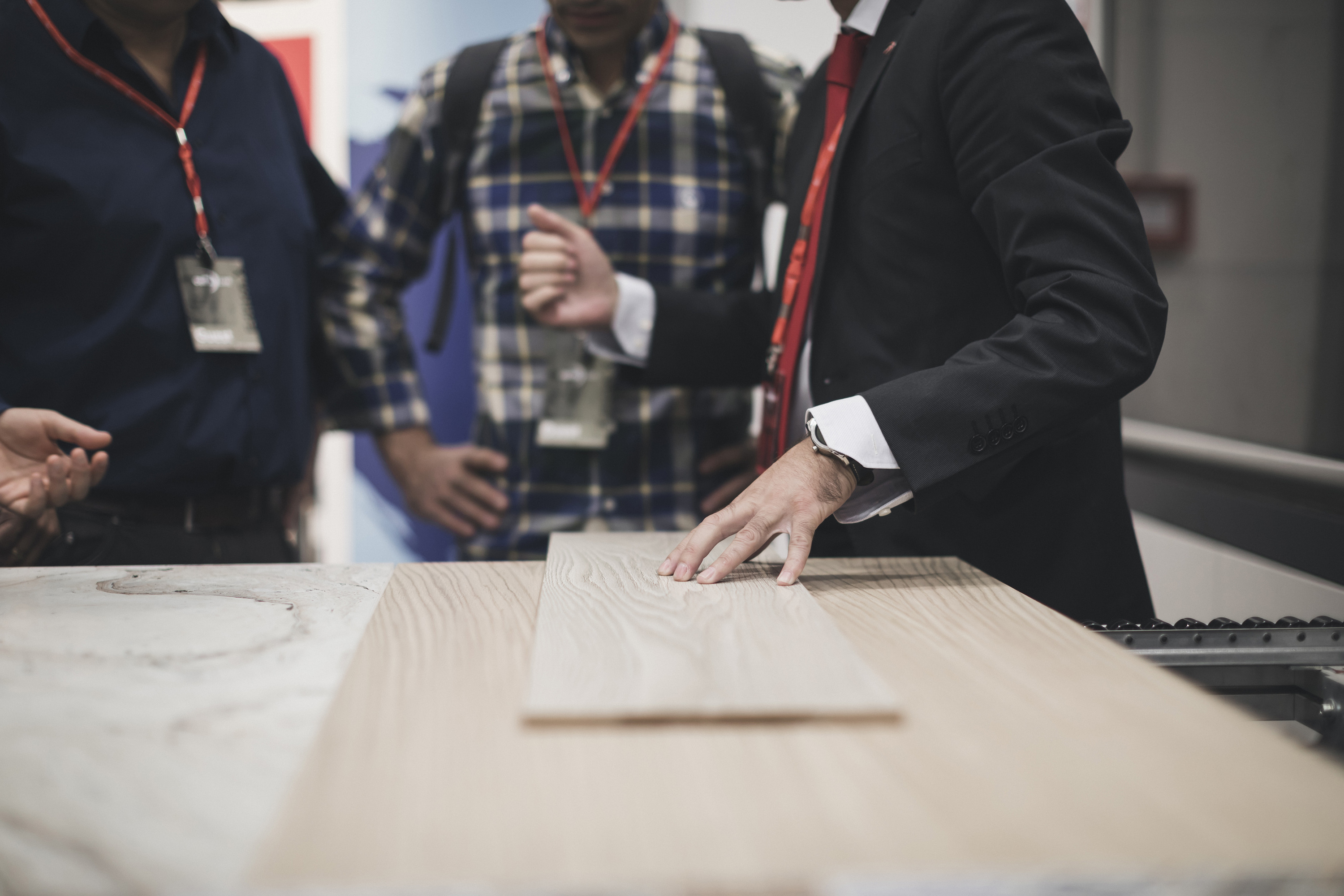
Connect
Frequently Asked Questions
Frequently Asked Questions
High flexibility in terms of output rate and choice of cycles/processes according to the line make-up.
Zero solvent emissions thanks to 95% use of products with high dry residue (UV) content.
Possibility of using the roller technique for any application on all flat surfaces.
- Handling large volumes. This technique is not for mass production.
- Economies of scale. Unit cost does not drop in line with higher volumes.
- Learning curve. Many end-users are at the start of the learning curve and need to develop some skills and knowledge to exploit the technologies. We can support you.