Helping HIB boost production volumes of automotive componentry
Project Data
Customer:
HIB, a company of the NBHX TRIM GROUP
Country:
Germany
Media Video:
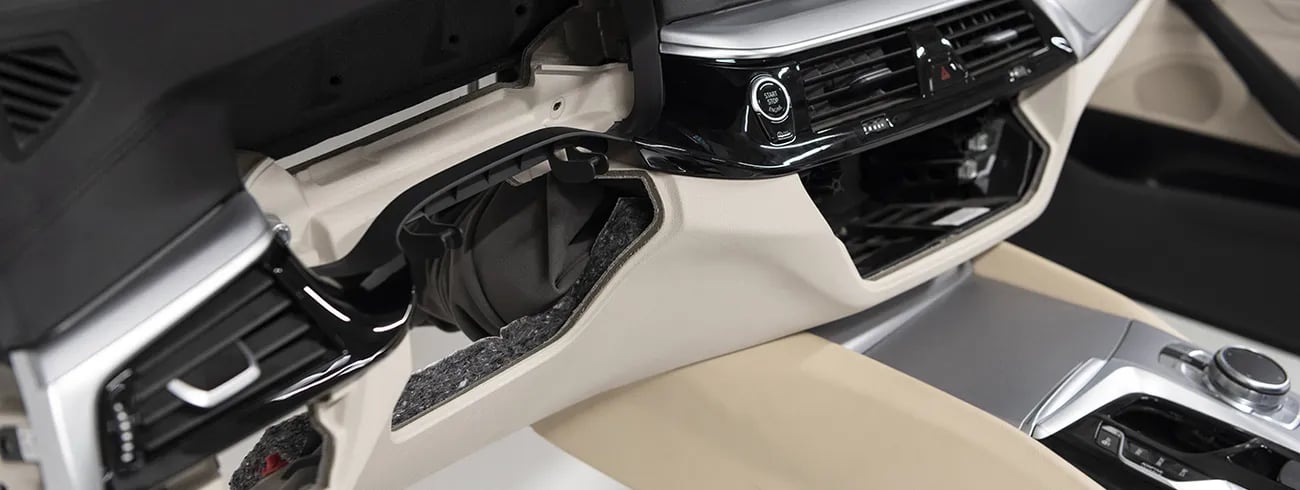
Automotive is synonymous with fast-moving, top quality. When we met HIB, a company of the NBHX TRIM GROUP, world leader in innovative surfaces for automotive interiors, the best way to achieve the required target was to exploit our broad experience and technical capabilities to provide an unbeatable solution.
NBHX TRIM GROUP employs 5,500 people around the world serving OEM customers and Tier One suppliers. The company is part of a larger concern founded in 1988 producing injection-moulded thermoplastics for interior and exterior decorative trims, instrument panels, exterior mirror assemblies, chassis accessories, and electrical and HVAC components for several major car manufacturers.
Requirement
Based in Bruchsal, HIB manufactures and delivers dashboards and the central console blocks for a premium vehicle brand. The company was looking for a partner from whom to purchase a turnkey solution for a brand new painting line, a critical step in the production process for the parts, in order to deliver on time to the car manufacturer. Once ready, the products are dispatched directly to the assembly lines and need to be faultless and must respect the quantities required.
Solution
Cefla Finishing gathered its key experts and configured a flat bed line with a non-stop conveyor. Parts enter the line from a Mito equipped with CO2 snow cleaning capability to prepare the surface. This is vital as the products are essentially “piano black” which is a high-quality glossy finish. Spray coating is then performed by an iBotic twin-arm Cartesian robot. cTracker software tracks pieces, recording data to analyse productivity, to memorise relevant information for component tracking and to implement production changeovers regardless of the manufactured parts and without emptying the line.
Benefit
Cefla has enabled HIB to achieve a 20% rise in production volumes, compared to the expected target, preserving competitiveness and facilitating on-schedule deliveries. Expected output and quality were reached thanks to our proactive approach, involving a dedicated team closely following the customer’s specifications, listening to their desire to improve performance and our constant presence until the line reached the pre-set targets.
When asked what the principal benefits were of working with Cefla, the customer replied: “20% increase in production at a fair price. The automotive industry usually has critical requirements regarding quality, productivity and scheduling. Working with Cefla we were able to define the solution, develop it and commission it together. Every stage handled with the same company, a turnkey solution which will also benefit from a global technical service network.”