What is an edge coating system?
Edge finishing is carried out with special equipment able to perform several actions:
- coating
- filling
- sanding
Advantages
Edge coating: advantages
Edge coating can respond to several needs, on a case by case basis:
- Improve the appearance of the workpiece.
- Deliver a personalised finish in terms of colour and texture.
- Coated edges enhance product quality, increasing product value.
- Coated edges ensure greater resistance and water tightness, for example if the surface is exposed to steam or water.

Finishing line for panel stacks
Painting 'stacked edges' is still very much in demand on the market, many high and low-productivity lines need such a solution to complete the painting process.
Usually developed for water- and solvent-based products, the line allows the complete painting process to be handled fully automatically by anthropomorphic robots, thus reducing all manual steps.
The certainty of iGiotto's repeatability allows full control over productivity, the quantity of paint applied and the resulting quality of the final product.
Below are some furniture industry-specific application areas and finished products
APPLICAzioni

Panel edges
Edge coating technologies
The edges of panels can also be coated by a Cartesian spraying robot such as iBotic, equipped with guns with movement about 5 axes, programmed to coat the edge of a panel fed through the spray coating area in "tracking" mode.
iBotic is a high output solution that guarantees both an excellent finish quality and a superior level of flexibility.
Generally speaking, roller coaters only coat flat surfaces. However, rounded edges can also be effectively processed provided the equipment includes a soft roller.
Edges (straight or with small radii) can therefore be coated by also using roller coating technologies. Our patented soft vertical roller automatically adapts to the shape of the edge without needing any extra equipment.
Another commonly used technology, vacuum coating is probably the most widespread method, not only to coat but also to seal edges, protecting them from humidity.
Our vacuum edge coating solutions include Talent, a patented vacuum system to seal parquet floors. The following products are compatible: water-based lacquers, UV curing water-based products, UV-100%, sealants (wax, paraffin, glue).
Specially developed to handle foils with thicknesses ranging from 0.1 to 2 mm and a printing width of up to 500 mm (19.7”), our industrial digital printing solutions also respond to some edge coating needs.
These are specific and customized solutions that should be evaluated together to identify the best one to meet flexibility, productivity and quality goals. For this reason, we are available to discuss with you how industrial digital printing can help you respond to edge finishing requirements.
We have chosen to combine coating and filling with sanding of flat and raised panel edges to offer a one-stop solution, providing a cost-effective, top-quality alternative to manual processing. Our Smartedge allows the edges of MDF, veneered and solid wood panels to be filled, sanded and coated with a single roller coating system, or using a patented "vacuum" injection technology.
We are well aware that edge processing affects the entire panel coating process and should therefore be considered critically important. Efficiency for large-scale production, flexibility for just-in-time jobs and consistently high quality are three top priorities in the panel finishing process.
Focus On
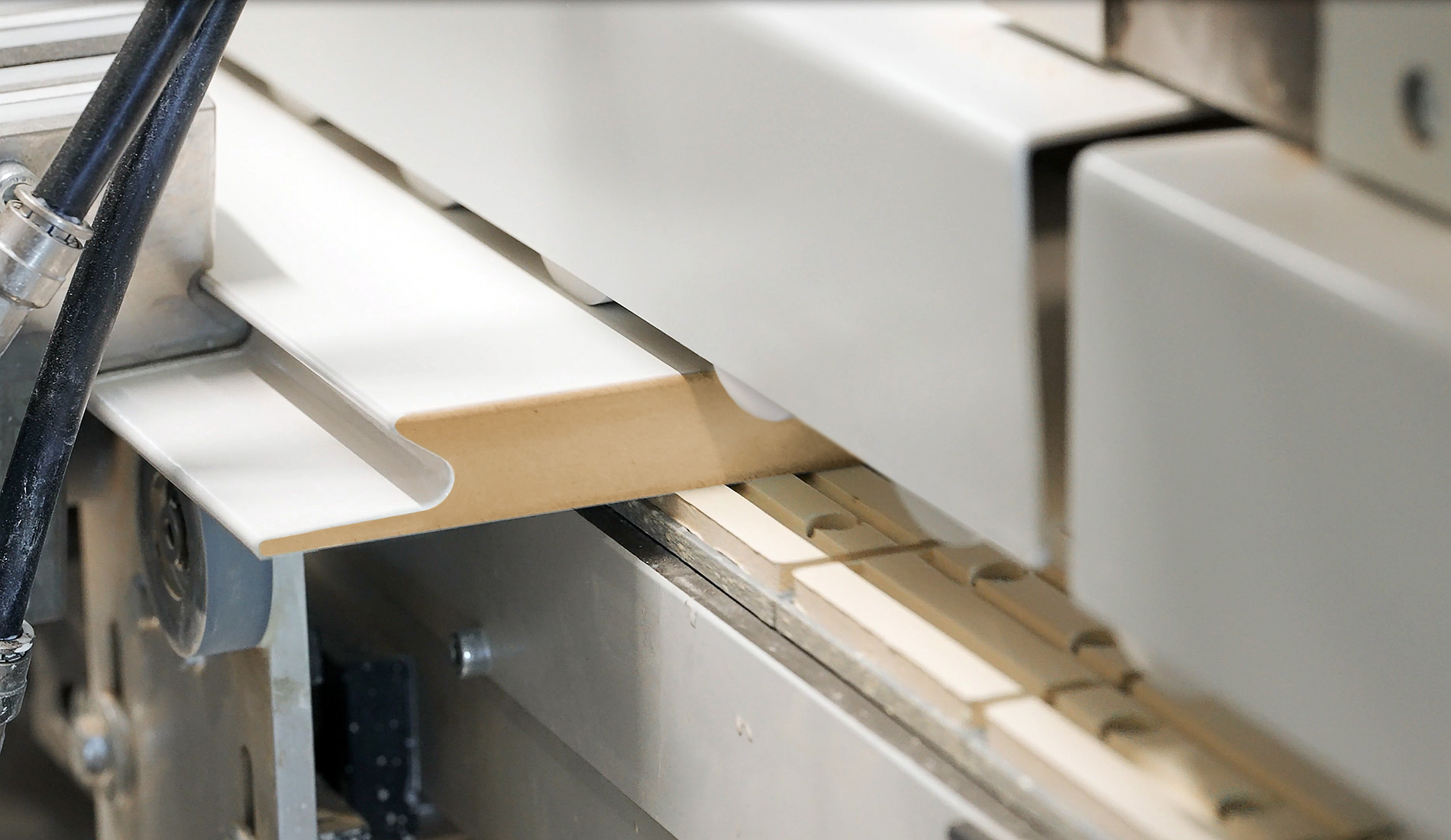
Top speed with Edge & Go
Edge coating, particularly when carried out with Smartedge, relies on our patented Edge & Go system, consisting of an application head with interchangeable straight or shaped slats to coat any type of edge.
Edge & Go lets you change over to differently shaped edges without having to turn off the vacuum tower. Switching from a straight edge with a 3 mm radius to a J-Pull handle edge, for example, takes less than 15 seconds.
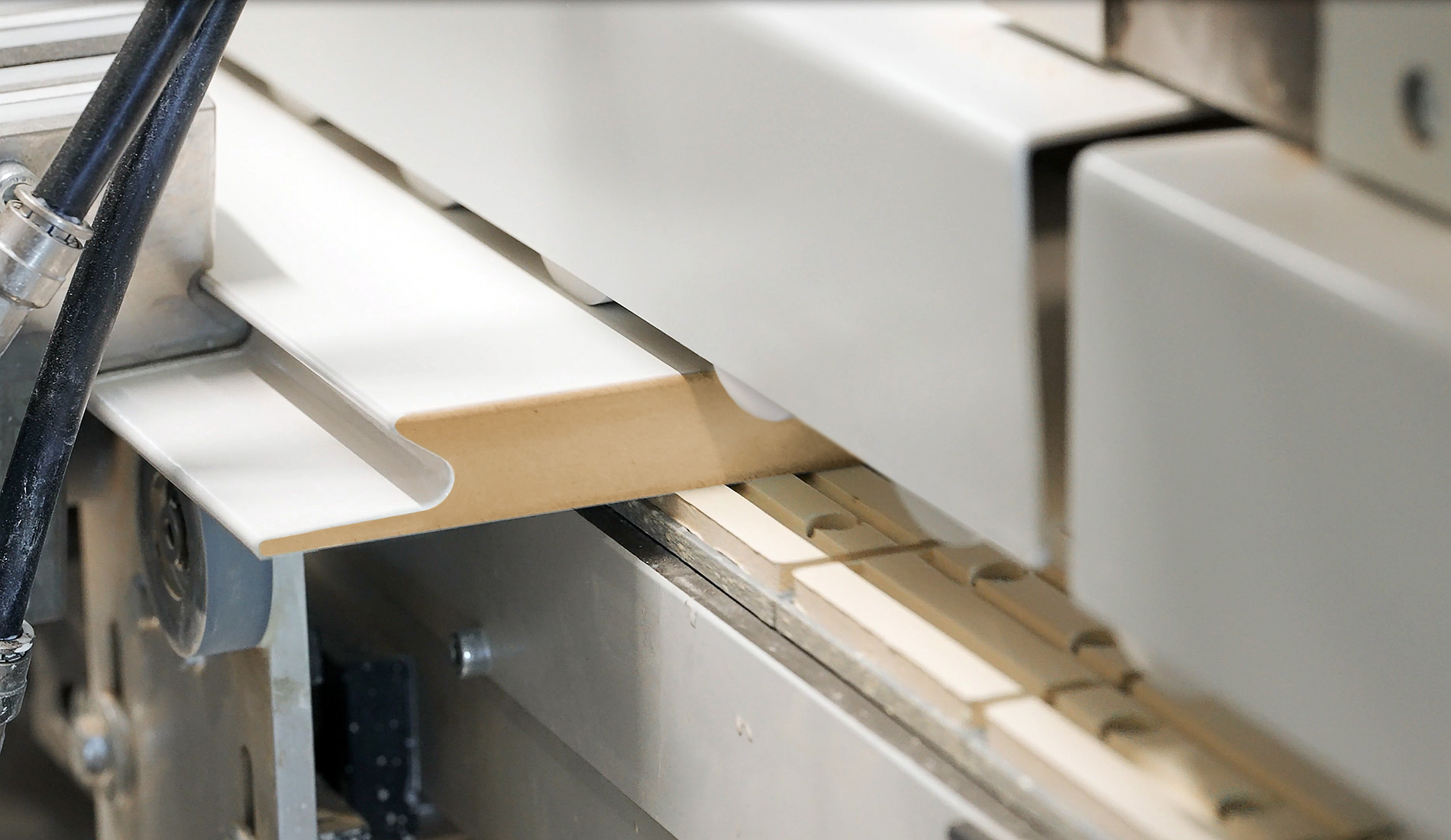
Roll-to-roll digital printing line
One way of achieving maximum personalisation and minimum waste is with industrial digital printing technologies. Complete lines using reels, with or without a digital white base, that are fed into and through a JP Single-Pass Roll-to-Roll digital printer enhance productivity and allow manufacturers to customise their products with decorated PVC applied to panel edges.
An eco-friendly technique, the digital printing process can be completed with roller coaters and curing ovens. Our machines also include innovative features such as the web-control device, the humpback design, and are easily cleaned and maintained as you will see in the video, which illustrates a typical edge-coating line implementing a digital printer.
Discover our edge coating machines
Machines
Case studies
Case study
WHITEPAPER
Do you know how to work around bottlenecks and other edge processing and coating issues?

Learn More
MAGAZINE
Are you looking for the ideal solution for your coating line?
All you have to do is fill out the form and contact us to obtain support from our experts.
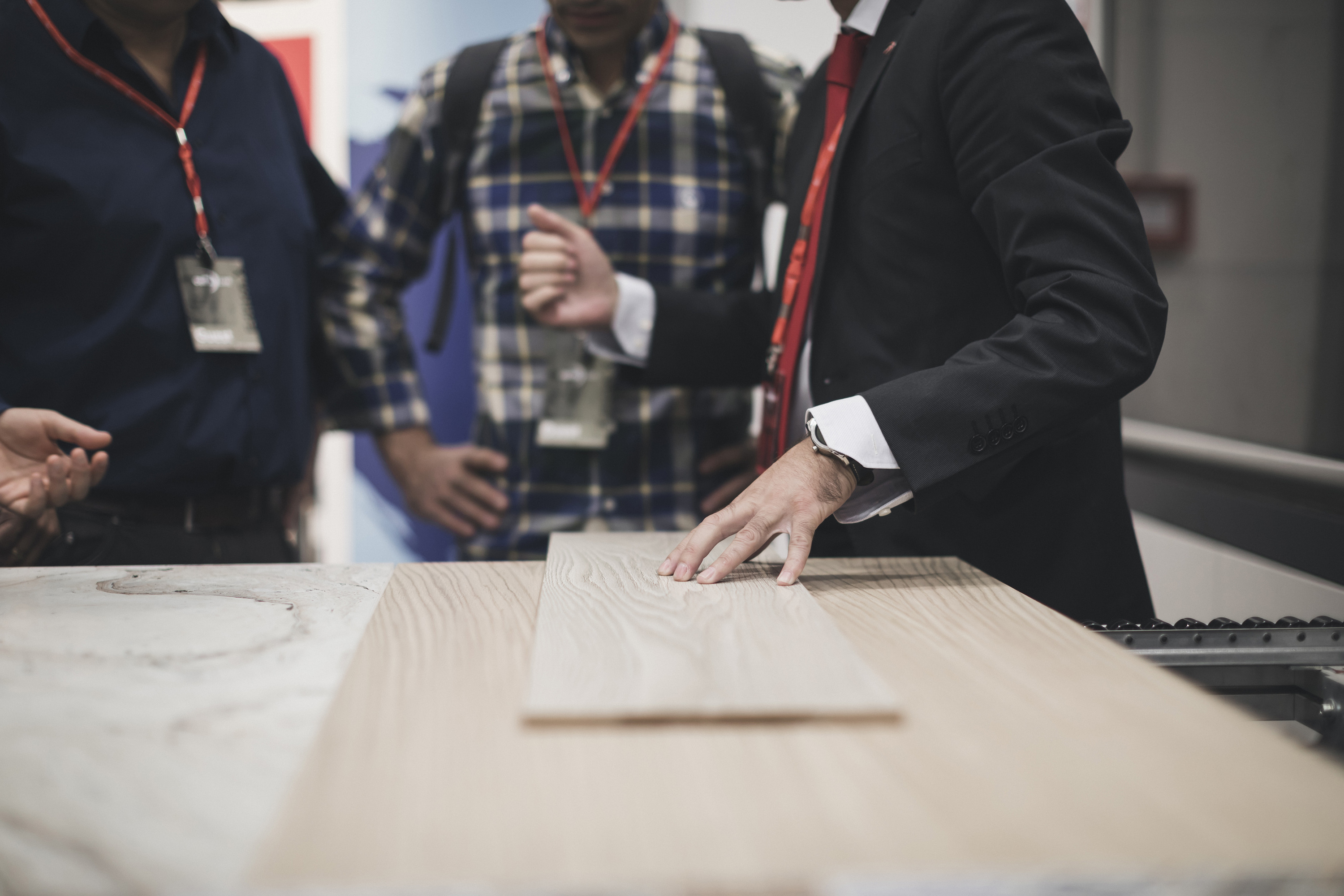
Connect
Frequently Asked Questions