Just look around you.
That’s all you have to do to see the results of our work
Many of the surfaces around you were made with Cefla Finishing machines. They are all around the places where you live or work, used as object coatings or parts of your car.
Where we are: always by your side
6
production sites across 3 continents
8
international branches
10
authorised centres worldwide
Cefla finishing
Our strengths
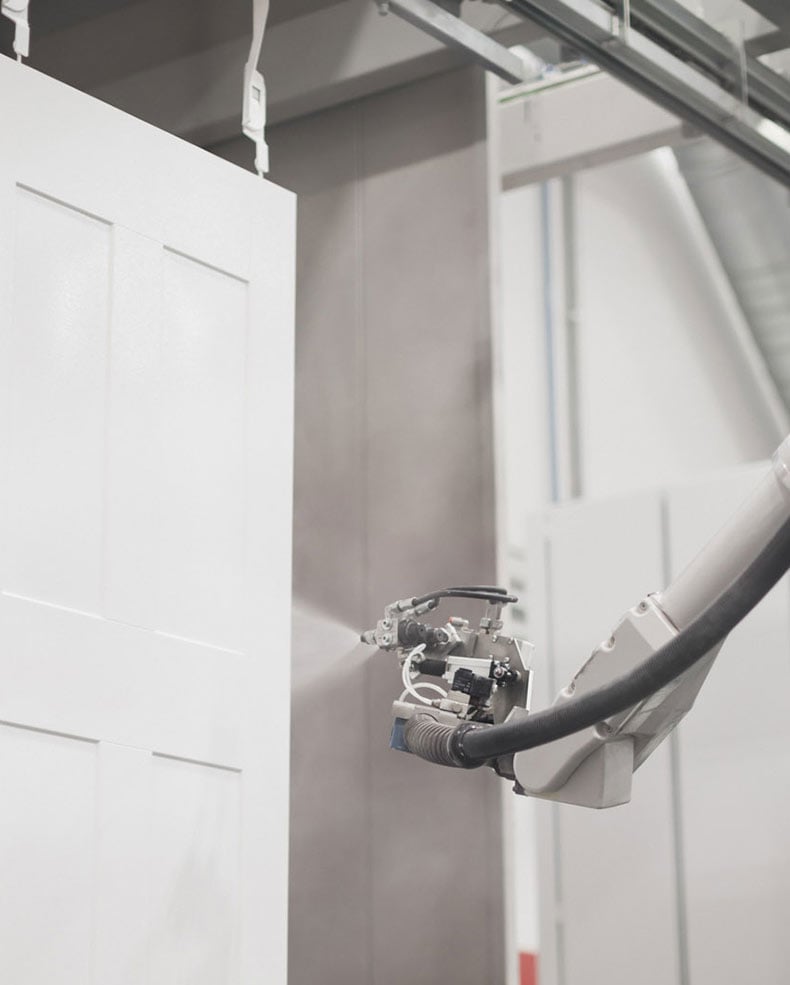
Innovation
The Cefla Finishing and Düspohl brands have made innovation our greatest strength over the years. We have developed more than 200 patents. That’s why our solutions guarantee the best market performance.
Discover moreService
The Cefla Finishing Service is an on-site and fast service which can count on software designed to help manage remote assistance, an extensive network of branches and authorised service centres. No matter where our customers are based, they can request high-quality training courses, spare parts and service at any time.
Discover moreSustainability
Our experience in many different sectors has allowed us to acquire a broader know-how through which we enhance efficiency every day. We optimise every single step of the finishing process to decrease energy use and constantly reinvent technologies from a green perspective.
Discover moreShaping the future of finishing
We design complete and customised finishing lines. We help our clients to embellish a substrate, providing it with unique characteristics.
Discover moreWhat industry are you interested in?
Our customers range from well-known companies in the construction and furniture industries, to manufacturers of home appliances and other durable goods as well as companies operating in the packaging, automotive and aerospace sectors. Which industry do you work in?
Cefla LAB: Where completely new ideas and solutions come to life
A place where the most innovative technologies are studied, innovated and tested. Where customers and paint manufacturers experiment with new solutions and create business opportunities every day.
A variety of packs to meet different support needs.
On-site support by qualified technicians
Digital technologies and processes, analysis and monitoring
Simulation, training and virtual reality
-
Physical
-
Digital
-
Virtual