Your future-proof Smart Factory
Local service, quick delivery of spare parts and technology: with Cefla Finishing you turn your company into your own efficient and always connected Smart Factory.
We know how time is critical in a high-productivity environment.

Service near you,
wherever you are
Cefla Finishing service is always close to you, thanks to software designed for remote assistance, an extensive network of branches and authorised service centres.
No matter where you are, at any time you can request high-quality training courses, spare parts and support.
Spare parts in 24-48 hours
Spare parts for our solutions are stocked in Cefla Finishing warehouses in Europe, United States and China. Over 20,000 different part numbers are ready to be shipped and delivered to you in 24-48 hours*.
Thus, your production will be back on track in a very short time.
*Availability within 24-48 hours is guaranteed only for parts in stock.
Take your business into the future
On-site support by qualified technicians
Digital technologies and processes, analysis and monitoring
Simulation, training and virtual reality
-
Physical
-
Digital
-
Virtual
Preventive maintenance
No unforeseen events, just efficiency, reliability, and predictability. We offer custom maintenance services to help you get the most out of your finishing line.
Asset Protection
Programme
To avoid any unexpected event, choose our all-inclusive pack. We'll draw up an accurate budget covering all preventive and extraordinary maintenance tasks, so you will know maintenance cost in advance.
Request more information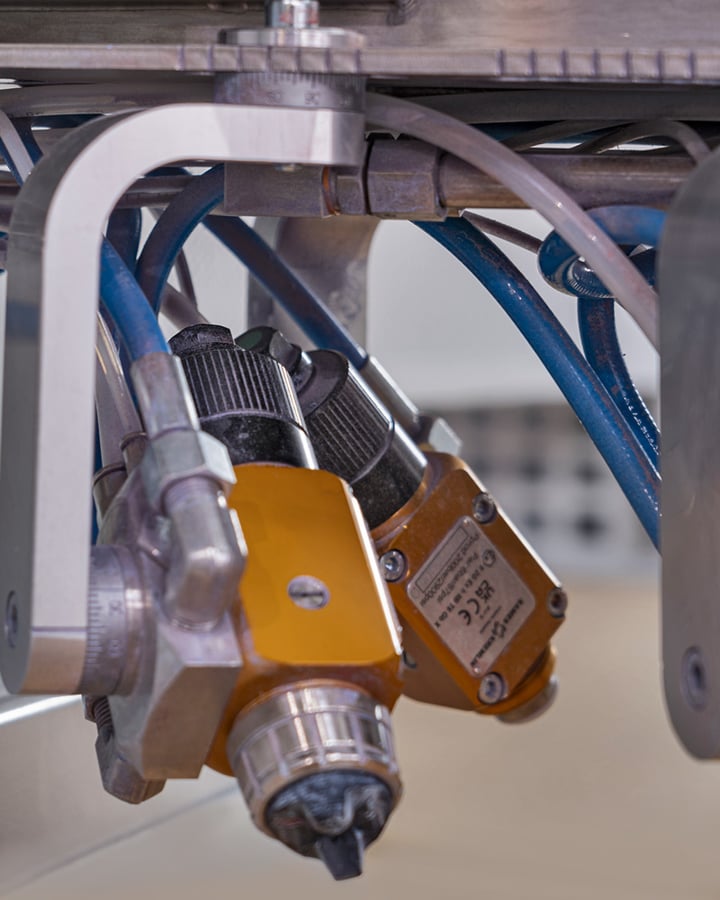
Rechargeable Preventive
Programme
If, instead, you prefer a flexible pack and consumption-based costs, opt for the modular program: flexible and customised according to the desired intervention frequency.
Request more information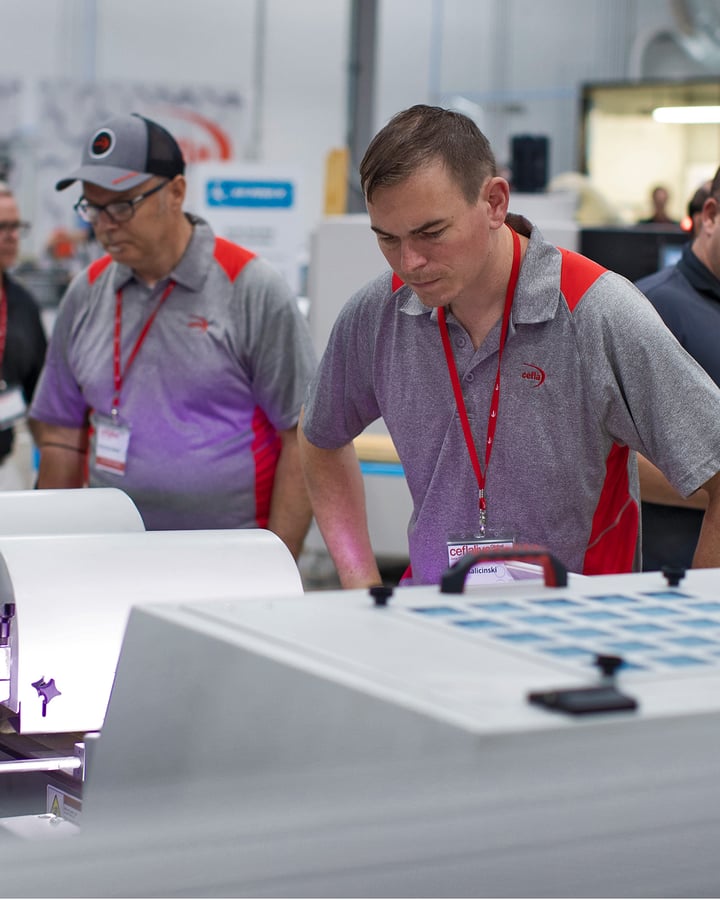
Frequently Asked Questions
Frequently Asked Questions
- set up and check the entire line from a single point
- trace workpieces on the line
- export alarms/production reports
- exchange information with your internal company systems.
- show a realistic 3D configuration of the line layout: a sound, reliable picture made up of measurements, 3D imaging and objective data.
- provide accurate line operation simulation: to prevent problems, avoid machine downtimes and have more general information right from the design stage.
- simulate real productivity and consumption: finding the best configuration gives you a realistic forecast of the situation, also in terms of productivity and energy/heat consumption.