What is a roller coating system?
A roller coating system generally consists of roller coaters located downstream from UV ovens in succession, with an upstream sanding machine. These coating lines can be customised to specific requirements, ideally for manufacturers who need to process the same large-volume production batches repeatedly.
They can also be designed to offer as much flexibility as possible - e.g. for finishing subcontractors who need to change from one colour or thickness to the next while limiting downtime.
Most roller coating lines can reach up to over 100 metres in length, taking up a lot of floor space, and need to be managed efficiently.
features
Main characteristics of roller coating systems
Efficiency, user friendliness, accessibility and control over the coating process are the main requirements of our customers.
- Setting up a coating machine must be simple, as operators are not always skilled or have little experience of roller coating lines.
- Downtime has to be reduced in every possible way, so that production efficiency accelerates the return on investment.
- Equipment must be easy to access, to ensure that any maintenance tasks or cleaning operations can be performed rapidly.
- Control over the coating process, in terms of lacquer consumption and coating quality evaluation, needs to be performed and adjusted if required in the shortest possible time. Having to stop the line to adjust coating machines individually is counterproductive.

Where can roller coating be used?
Sectors
Campi di utilizzo
Below are some roller coating application areas and finished products
APPLICATIONS

Bedrooms
Focus On
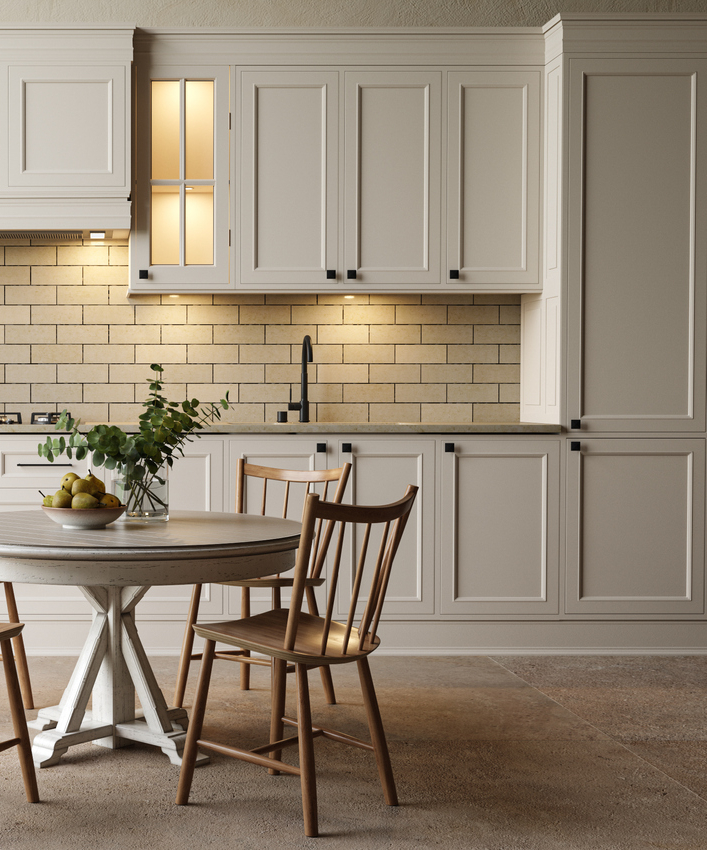
Raised panels: trends that we are both following and driving
In addition to being able to process poorly calibrated panels, we have developed a roller coating system to process slightly raised panels, for companies that are looking to expand their field of action achieving even greater flexibility. A soft coating roller combined with an improved lifting system based on 4 screw jacks to ensure greater stability and sturdiness can coat efficiently and economically.
Discover more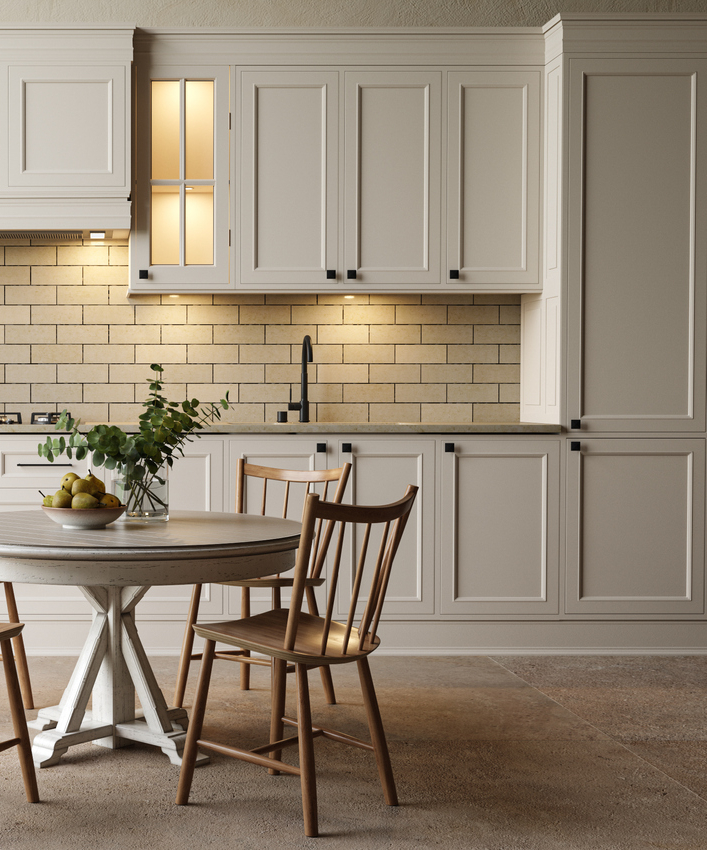
Requirements of efficient roller coating systems
What are the assets of a modern and efficient roller coating solution? We have identified four:
Accessibility is a very important requirement. Cefla Finishing coating machines are designed to facilitate access when any maintenance work is required, saving time between production runs.
In particular, the coating process - including lacquer consumption data based on applied lacquer weight, production speed and panel thickness - can be monitored automatically without having to individually check each machine in the line. This means that qualitative and quantitative adjustments can be made on the go, reducing downtime to a bare minimum.
There are user-friendly HMI interfaces on each machine of the roller coating system, which simplifies the programming process. Colour changeovers are fast, which boosts flexibility, and semi-automatic cleaning systems can be included to minimise time and solvent requirements.
Visual feedback is also an asset linked to machine accessibility. At Cefla, we have developed this aspect even further, by enabling process visibility thanks to see-through protective guards built into our machines. Customers can now rely on immediate visual feedback from the process without having to stop production to carry out inspections.
One of the issues faced by user companies concerns the quality of the panels to be processed. In many cases, the panels are poorly calibrated - which has an impact on roller coating process control. We have been able to solve this issue with a floating system able to efficiently process flat panels with uneven surfaces fed through the machine. This enables coating consistency despite poor calibration and reduces the chance of rejects due to below-standard quality.
One aspect we feel confident about concerns quality, despite this being a highly subjective factor. We have the world’s largest finishing laboratory, where every process can be tested using our customers' own products, substrates, primers and lacquers. The best way to achieve the desired outcome is to run a full production test in our LAB. This helps us optimise all the working parameters to ensure output repeatability once the line is installed and starts running.
Discover the LABDiscover the roller coating systems designed to obtain these results
machines
Case studies
case study
WHITEPAPER
How to optimise roller coating technologies for a growing variety of products and substrates

Learn More
MAGAZINE
We’ve been innovating in the surface finishing field for sixty years.
Tell us where you want to go and our finishing experts will help you get there.
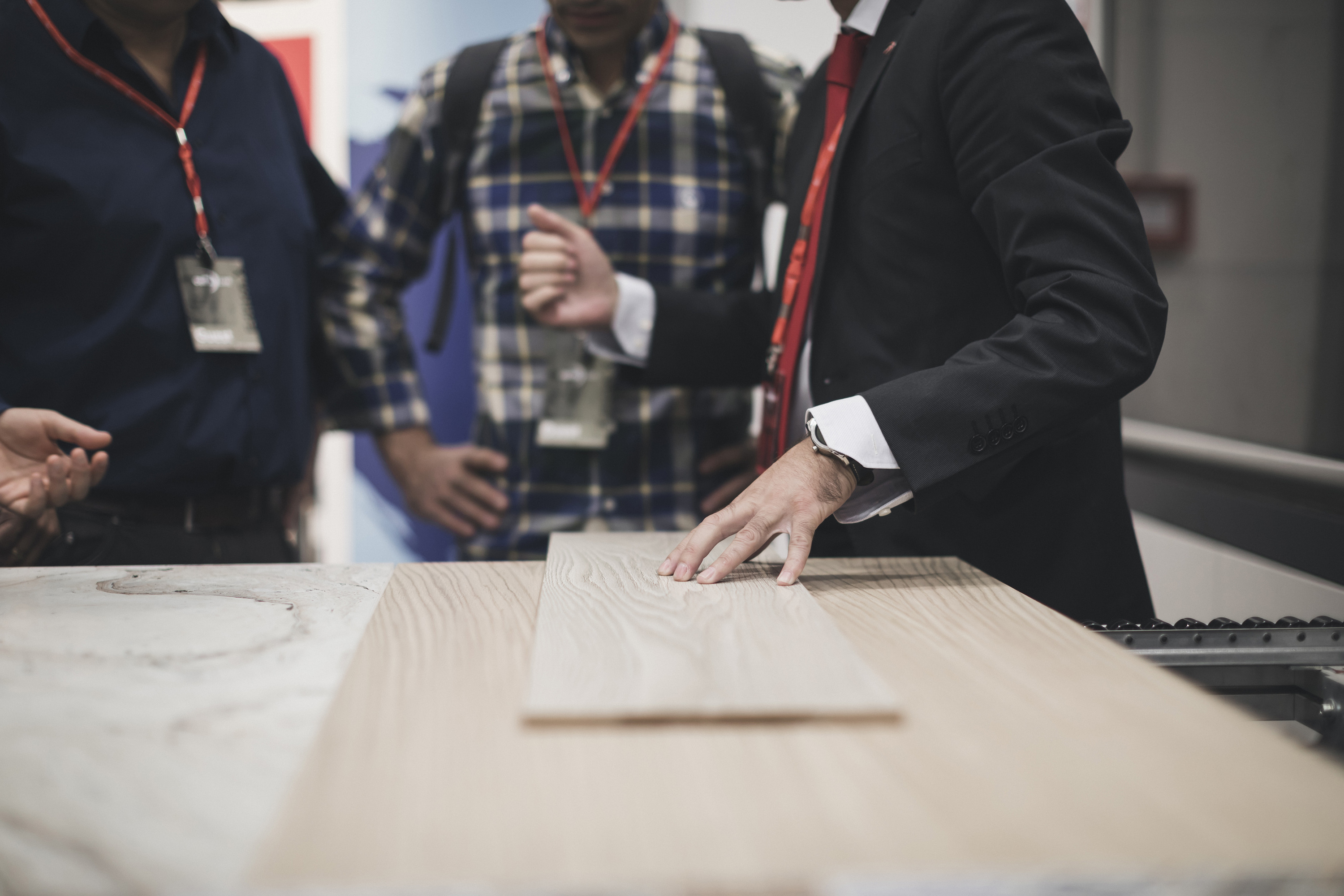
Connect
Frequently Asked Questions
Frequently Asked Questions
Examples of products suitable for roller coating:
- cabinet doors
- parquet
- doors
- wood and wood-based materials
- glass
- cork
- plastic
- fibre cement
- metal
- roll-to-roll for edges etc.
High flexibility in terms of output rate and choice of cycles/processes according to the line make-up.
Zero solvent emissions thanks to 95% use of products with high dry residue (UV) content.
Possibility of using the roller technique for any application on all flat surfaces.
The quality of the paint finish is highly subjective. However, opacity and gloss, and obviously, the degree of application, can all be rated.
Today, thanks to the SmartCoater PRO series and the choice of specially designed rollers, in some cases it is possible to apply UV primers on cabinet doors and specially shaped doors. This refers to primer application. After the intermediate sanding phase, finishing is carried out with spray coating machines.
Yes. It often happens to have coating lines consisting of roller coating machines for primer/insulating product application followed by spray coating machines for finishing.
In roller coating machines, 100% UV acrylic products, as well as water-based products, can be used resulting in a highly sustainable finishing process.
Yes. Normally, on small, low-output lines, the machines are flushed to carry out colour changeover. Otherwise, multipurpose machines are added to the lines to be able to manage colour changes very quickly.