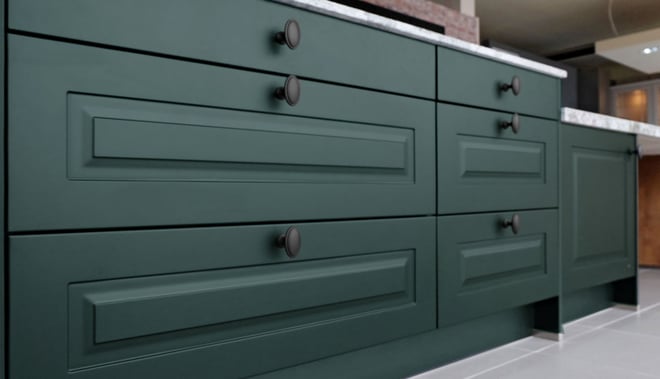
Deep matt surfaces, beautiful to look at, pleasant to the touch and resistant to scratches and light: this is what can be achieved with excimer technology, the new frontier for the processing and finishing of flat and raised panels.
Advantages of excimer technology
Procedures based on this drying technique, in particular UV ovens, effectively respond to the need for matting items characterised by three-dimensional geometries - typically doors and panels. Not only that: they also meet the need to reduce energy costs and the environmental impact of processing. This is thanks to the efficiency guaranteed by the short-wave UV curing process, which does not require the use of traditional matting agents.
But let's proceed in order: before delving into the advantages, here's a review of the characteristics and best uses of excimer technology.
Excimer oven technology for high quality matt surfaces
We are all aware that the market tends to attach more and more importance to the sensory aspects of home furnishings. The tactile experience, in particular, is becoming a key factor in the choice of furnishing accessories. Soft-touch finishes are increasingly popular: not only do they enhance the pleasure of making contact with an item, but they also increase the item's surface resistance to scratches and wear.
To achieve this type of finish, manufacturers need a solution that effectively processes all sides and edges of their product, maximising quality and cutting costs where possible.
Excimer ovens are able to treat more complex shapes than plain flat panels, and they are therefore ideal for creating high-quality matt surfaces.
THE MOST INNOVATIVE FINISHING SOLUTIONS
Discover how highly advanced finishing solutions can enhance your competitiveness.
Excimer matting: processes and results
But how does the excimer matting process actually work, and what steps allow users to obtain captivating, durable and abrasion-resistant surfaces without the need for extra chemical agents?
Liquid excimer coating is usually applied with roller-based techniques: the items to be finished are coated and then conveyed to specially provided ovens and subjected to a hardening procedure using short-wave UV light in the absence of oxygen. This is the step that triggers the surface curing process of the excimer liquid, which decreases in volume as it dries.
The resulting effect is the creation of micro-folds of varying thickness which in turn will cause surface deformation. This process, while being invisible to the naked eye, is powerful enough to deflect and diffuse light, generating a visually matting effect and an extremely pleasant haptic experience.
The process ends with hardening of the surface coating, usually obtained by irradiation from a UV dryer.
What can excimer ovens achieve?
Let's now go into more detail and analyse the results that can be obtained thanks to conventional excimer ovens: these machines are used as mentioned above to carry out short-wave UV curing of flat panels in an oxygen-free environment.
In order to obtain high-performance surfaces with a soft-touch feel, the lacquer used must be treated in such a way as to achieve a deep matt finish, up to 5 gloss (on a gloss scale ranging from 0 to 100). This step is essential in order to obtain another effect that is increasingly in demand, known as “anti finger print” finish: thanks to a slight wrinkling of the surfaces, the excimer technology effectively prevents the formation of fingerprint marks. This is exactly what the line proposed by Cefla Finishing allows users to achieve. It is a line specially designed for manufacturers who wish to reap all the benefits of excimer technology.
UV-R: the integrated solution ensuring maximum versatility
UV-R is a UV drying oven that integrates all the machine elements (conveyor, UV body and control panel) into a single body. It is the ideal solution for all those seeking versatility and user friendliness, without wishing to compromise on the guaranteed quality of the end result.
Exydry: the future of excimer ovens
For the most demanding users, Exydry is the perfect solution when it comes to processing 3D items which typically need to have matt edges that are as strong as flat surfaces. The result of an internally developed R&D project, Exydry by Cefla Finishing is an innovative solution that allows users to obtain a matt finish by treating the workpieces before cross-linking is completed, easily achieving values below 5 gloss.
In panels treated and dried in Exydry, these values are combined with extremely high surface resistance - not to mention the fact that the amount of nitrogen used to wash away oxygen from the X, Y and Z axes of raised panels is significantly lower than in conventional excimer ovens.
Exydry: How does it work?
Featuring three patent-pending technologies, this innovative system is able to process, for example, cabinet doors coated by oscillating sprayers or robots. The system design allows for a continuous flow of raised panels through the oven, removing all oxygen without ever needing to stop the plant.
The key benefits obtained, as mentioned, are not only the improved finishing quality and the ability to obtain this level of quality on three-dimensional objects, but also the reduction of production costs thanks primarily to optimised nitrogen consumption.
Excimer matting technology: why choose Cefla Finishing
With 60 years of experience in the design and production of finishing systems, Cefla Finishing is the ideal partner with whom to develop an innovative and tailor-made solution, particularly when it comes to innovative techniques such as excimer matting.
We provide customers not only with an expert team of specialists capable of identifying the right technology for the task at hand: we also, and most importantly, work to ensure seamless integration of new machines into existing processes. After assessing products, needs and business goals, we work closely with customers to define a plant development roadmap that can also include preliminarily plant testing at one of our Cefla Finishing labs.
LOOKING FOR THE IDEAL COATING LINE SOLUTION?