
Working with a sprayer or a robot with a belt that allows paint recovery means cleaning the belt regularly to remove any trace of the applied product. The more paint you recover, the less you spend.
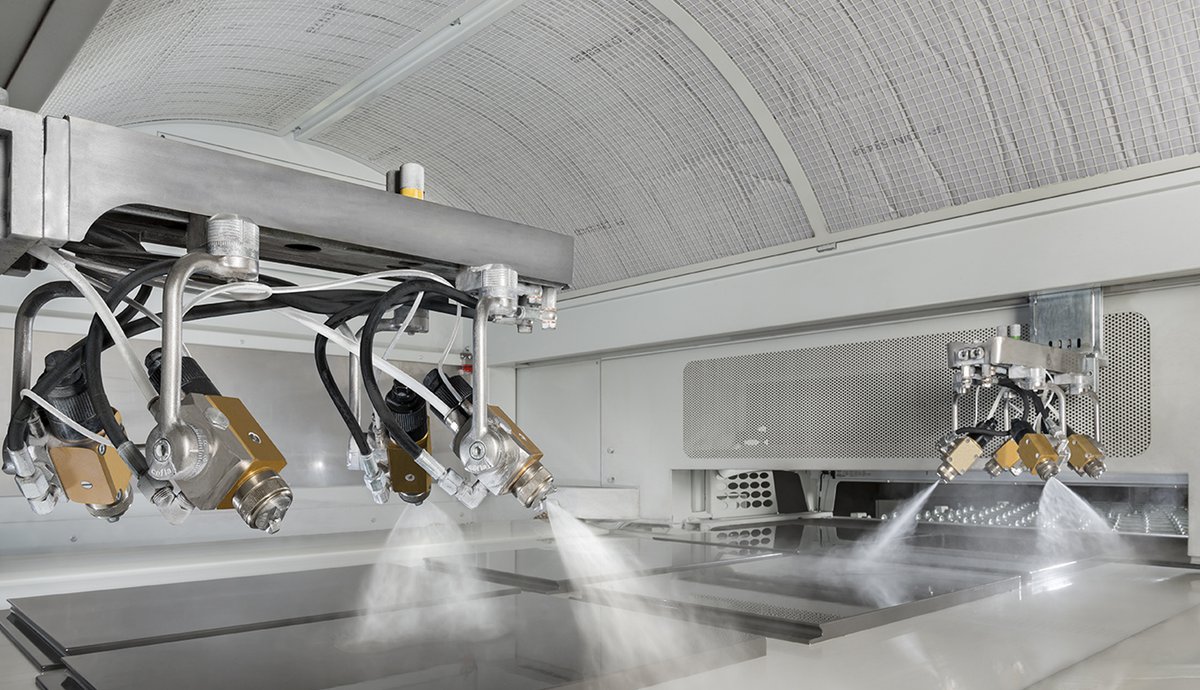
Of course, if you say patented savings everyone wonders what you’re talking about. How can you patent a saving? Well you can’t, but what you can do is patent the way you reduce costs and if the system you design saves significant amounts in the long term, well it’s worth patenting. We patented our spray cleaning technology so you can save money.
Working with a sprayer or a robot with a belt that allows paint recovery means cleaning the belt regularly to remove any trace of the applied product. The more paint you recover, the less you spend.
If your spray cleaning system is conventional, you will not only throw away a lot of paint, but you will also use a significant amount of detergent. Conventional systems also lead to rapid belt deterioration, either through the abrasion from belt cleaner blades or aggressive solvents.
A system ensuring maximum cleaning potential recovers more paint and enables you to use less detergent during running time. Less detergent means lower operating costs, it safeguards your equipment and ensures a healthier environment. On average ruined belts are replaced monthly, meaning a full day of downtime every 20 working days. This frequency can be avoided.
Our patented spray cleaning system can be fitted to our Roctre, Mito and Easy oscillating spray machines. You will benefit from:
- increased paint recovery
- detergent consumption which drops to around 50 litres per shift
- fewer production stoppages to replace belts
- minimal end-of-session cleaning times
- enhanced production efficiency