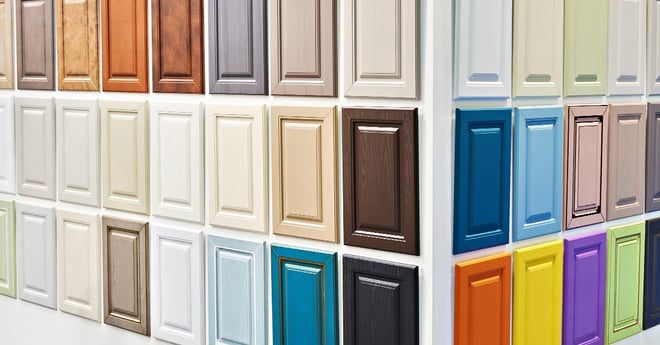
How to coat flat cabinet doors?
Edge finishing
Edge finishing is a crucial stage as it ensures doors have an impeccable appearance and long-lasting protection. This process begins with thorough sanding of the edge to prepare it for application of the primer and subsequent coatings. Cefla Finishing machines such as Smartedge allow for the application of primer and coatings in vacuum mode, ensuring even coverage. Each coating application is followed by controlled drying, which involves semi-curing in a UV oven. Summing up, the steps are:- Sanding: sanding the edge is the first step. This ensures proper preparation before application of the primer and edge finishes. Abrasive wheels or belts can be used.
- Primer application: the primer is applied on the edge using roller or vacuum systems such as Smartedge, the Cefla Finishing solution for edge sanding and coating.
- Coating applications: this involves two or more vacuum applications of transparent or pigmented UV coating, using a total of 180 g/m2 of product. Each application is followed by a gelling or UV drying process.
- Drying: after each coating application, a semi-curing process takes place in a UV oven; for pigmented products a gallium lamp is used.
- Sanding: the process ends with automatic sanding of undercoats using a sanding wheel or belt.
Spray coating
After vacuum-technology edge finishing, the panels are spray-coated. The process stages are:- Spray coating: application of a quantity of primer suitable for the type and density of the substrate. This is achieved using a sprayer such as iBotic, the high-capacity Cartesian spraying robot; iBotic can also process J-Pull profiles and standard flat panels. The robot can spray both flat surfaces and edges, obtaining a high-quality finish.
- Drying: the doors are then dried completely in a vertical oven. Omnidry is a flexible vertical oven: with its optional FLEXPRO function, it can automatically process pieces of different size and/or thickness.
Hybrid coating
Depending on specific production requirements, manufacturers can adopt a hybrid coating cycle that combines the best available technologies. Edges can be finished with Smartedge before coating the panel with Smartcoater Pro. Where doors have contouring, the latter can be equipped with a soft roller. Subsequently, a high-quality finish can be achieved by spray coating with robot systems such as iBotic or oscillating systems such as Easy or Mito. This hybrid approach provides the advantages of both technologies, ensuring excellent results on edges and flat or raised surfaces.Raised cabinet door coating
Let's take a detailed look at how to coat cabinet doors (for kitchens or other rooms) if they are raised. Raised panels are often spray-coated. This is because, until recently, roller coating technology was unsuitable for raised doors. However, roller coating has evolved and can now be used on raised panels such as kitchen cupboard doors, or any substrate with a groove shallower than 10 mm.
Smartcoater PRO is a roller machine equipped with a soft rubber applicator roller. This special roller not only performs the intended task: combined with other exclusive features on this next-gen machine, it also guarantees an even result.
Such features include a special stabilising framework for the application head that uses 4 screw jacks. This set-up exerts considerable pressure on the panels passing over the machine and, thanks to the floating pneumatic system (another exclusive feature that can be integrated into Smartcoater PRO), the applicator head follows the irregular contours of the panel; it also compensates for panels that have been insufficiently calibrated.
The raised cabinet door coating steps can be summed up as follows:
- Primer application: (35 g/m2) using Smartcoater PRO.
- Drying: in UV ovens with a gallium lamp for gelling.
- Roller coating: again, using Smartcoater PRO.
- Second drying: carried out under 2 gallium and mercury lamps.
- Sanding.
- Spray coating: to apply the final finishing layer, using spray-coating machines such as Mito or iBotic.
The advantages of coating cabinet doors with Smartcoater PRO
Coating raised panel surfaces with a machine that has a soft roller offers multiple advantages:- transfer is more efficient that with spray-coating.
- the process no longer requires sanding between undercoats.
- fewer handling tasks.
- all this results in shorter coating times.
- less coating and solvent consumption.
- shorter delivery times.
The perfect cabinet door coating partner
In conclusion, coating cabinet doors is a crucial stage of the finishing process as it significantly affects the quality, appearance and durability of the final product.
At Cefla, we’re proud to offer not just machines but complete turnkey solutions, tailored to the specific needs of each customer. Our goal is to provide furniture companies with close support, helping them set up production lines in a way that best matches their processes so they can maximise efficiency and deliver excellent finishes.
Talk to one of our experts to find out how we can help you achieve your goals