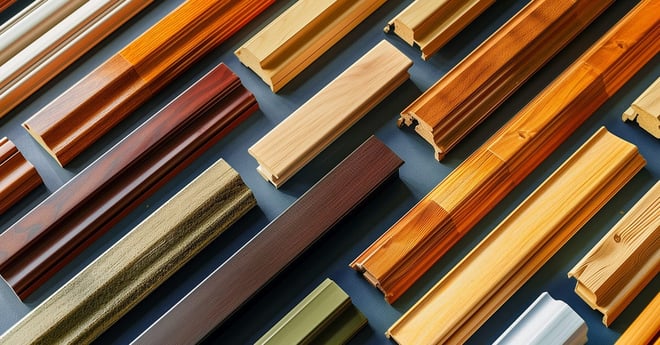
Wooden profile finishing is an essential stage of the production process as it confers quality and durability on a range of products that are becoming indispensable in the construction, furnishing and interior design sectors. Hence the increasing number of technologies and methods that can be used to complete this delicate process.
This, of course, means more choice: on the other hand, though, you need the right knowledge and skills to be able to select the tools that best meet your production needs.
The importance of profile finishing
Before looking at the most popular techniques, let's define the aspects that make profile finishing so vital to improving the visual appearance of a product and making it more durable and reliable.
A well-finished product is more attractive to consumers and provides a more satisfying tactile experience: consequently, it can have a significant impact on purchasing decisions. Consistent aesthetics among products, even those belonging to different lines, is essential for building brand identity and the consumers' perception of quality. Moreover, the fact that profile finishing provides scope for customised design should not be disregarded: different coatings and effects can create unique looks that meet individual customers’ preferences.
Meticulous profile finishing protects raw materials from the humidity, UV rays and temperature variations that can, over time, lead to deterioration and damage. This prevents problems such as warping, cracking and fading, increasing product longevity.
Last but not least is the issue of compliance with standards, especially for companies that operate internationally: many markets have clear standards on the finishes used in furniture, especially with regard to volatile organic compound emissions. Suitable finishing processes ensure compliance with such regulations, making products safer for consumers and environment-friendly.
Profile finishing technique types
From sanding to sealing, through coating and drying, there’s a range of technologies for obtaining an optimal finish. Let's examine, one by one, the techniques available on the market, and highlight their specific characteristics, advantages and fields of use.
Profile sanding: the first step towards a perfect finish
To begin with, the main benefit of sanding is its flexibility. To ensure freedom and simplicity of cross-section/size configuration, modern sanding machines feature sanding belt, wheel or brush units.
For example, the BPS range, specifically developed by Cefla Finishing for profile sanding, has two versions - with CNC or manual adjustment - to maximise adaptability to all profiles or panels, even those of limited width.
Vacuum technology for perfect profile sealing
Sealing solutions with vacuum technology are perfect for manufacturers who prioritise process efficiency. The most advanced machines, such as our Talent, deliver almost 100% transfer efficiency by applying a uniform coating with exceptional precision and speed.
Incorporating UV lamps allows the machine to perform the necessary curing process and is perfect for treating different substrates and processing wood.
Compatible coatings include water-based products, UV-curable water-based products, 100% UV products and various sealants. Zero overspray minimises coating and sealant waste and allows the machine to coat six sides in a single pass.
Spray coating: flexibility and precision
For those looking for flexibility and precision, in-line spray coating offers an increasingly compelling response. Featuring a system that guarantees continuous processing, our Performa is available in three different configurations to match the customer’s profile conveying system. Numerous spray guns allow the machine to process widths of up to 300 mm and apply pigmented products and water- and solvent-based coatings. This sprayer is also highly suitable for high-speed lines.
Alternatively, Flexispray offers a more economical, more compact solution that’s ideal for facilities with limited floor space. Designed to provide manufacturers who still use manual application with entry-level automation, it can finish items up to 240 mm wide (in certain conditions up to 300 mm) with up to six spray guns.
Profile drying: energy efficiency with the transverse kiln
Lastly, companies eager to achieve high energy efficiency can focus on optimising their drying technique. In this case, profile finishing is performed by machines able to dry coatings applied on low-width profiles or panels. For its most demanding customers, Cefla Finishing offers the Cross Oven, a modular solution that treats water- or solvent-based coatings by way of an insulated structure that makes the oven extremely effective and efficient.
Profile finishing: why choose Cefla Finishing?
60 years’ experience in the design and construction of automatic systems makes Cefla Finishing the perfect profile finishing partner, able to build innovative solutions around the customer’s individual needs.
Indeed, we provide customers not only with an expert team of specialists capable of identifying the right technology for the task at hand: we also work to ensure seamless integration of new machines into existing processes. After assessing product, needs and business goals, we work closely with customers to define a plant development roadmap that can also include preliminarily plant testing at one of the Cefla Finishing labs.
So all that remains is to put us to the test. Contact us and find out which profile finishing solutions will help you boost your line performance!
LOOKING FOR THE IDEAL COATING LINE SOLUTION?