
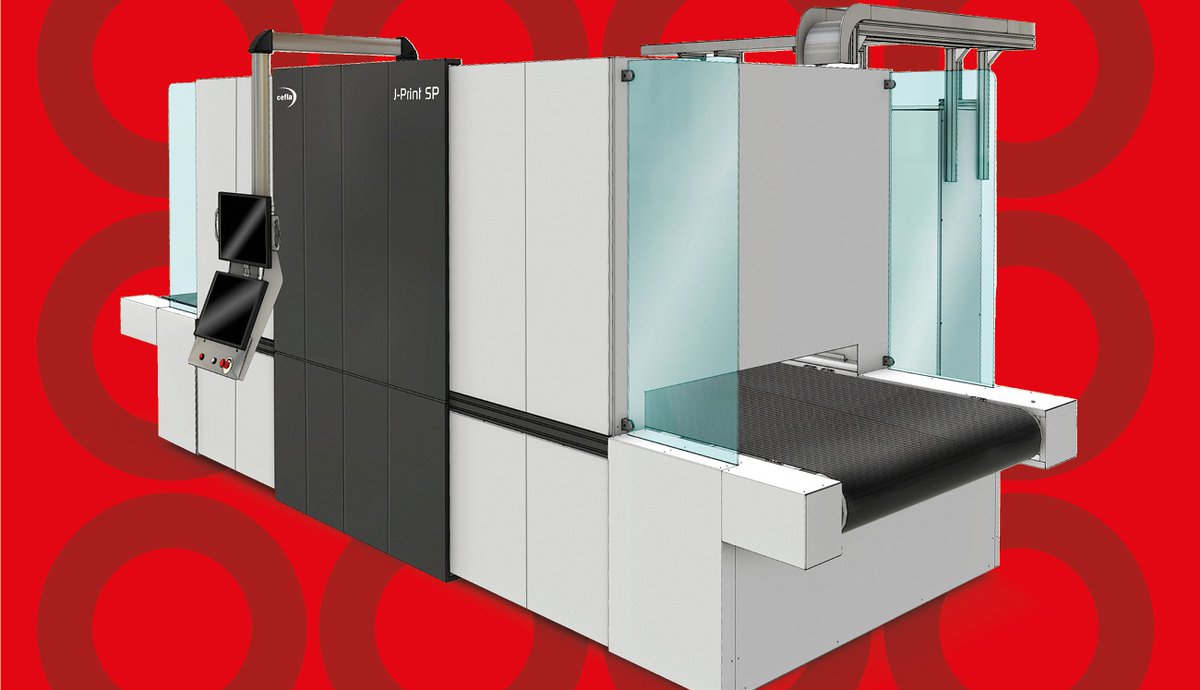
There are a number of issues facing many furniture manufacturers, such as lead times unable to cope with the increasing demand for personalisation. Small production batches are also a growing phenomenon that requires substantial flexibility. Another issue, when it comes to a high degree of personalisation and variability, is the difficulty in matching edge patterns and colours with the flat panel surface. Some manufacturers are overcome with stockpiles of engraved rollers and colours or hundreds of rolls of decorative paper, plus the need for stock service ensuring a number of replacement items.
Overview of the benefits of digital printing
Many of the abovementioned problems can be overcome with industrial digital printing. Apart from the equipment and the inks, all you need are the skills needed to deal with digital images and initiatives to promote a service your customers will immediately appreciate, such as:
- limitless customisation possibilities
- very small production batches (10 – 100 sqm)
- lead times go from a few hours to a few days
- reduced stock requirements
- virtually no stock service at all
And all of this can be said for both the decoration of a flat panel surface and the panel edge, so that the pattern and colours are perfectly matched.
Same image, same procedure, same inks if possible
Although it may not be the same company handling the decoration of the flat panel surface as well as the edgebanding, digital printing allows for a perfect match between panel surface and panel edge on the finished piece. Elaborating the digital image for both tasks is the first step. Using the same inks optimises the match, but may not always be possible depending on which inks each company adopts. Overcoming metamerism with digital printing of the flat surface as well as the rolls of edgebanding material is also much easier if the procedure and the inks used are the same.
The ideal integration to multiply your business opportunities
Industrial digital printing is a technique which fits seamlessly into a finishing line, speeding up the process, offering enormous flexibility and allowing companies to say “yes” to single pieces or minimal production batches. After sanding and primer application, the flat surface can be decorated with a digital printer followed by a transparent basecoat which precedes the finished effect that can be matt, glossy or even texturized (haptic effects), the latter also accomplished on a digital printer.
So much faster, so much simpler
One of the key advantages of this technique is the speed. A recent example illustrates the huge opportunities and how simple it is to achieve results which are unheard of using traditional decorative techniques. For an international fashion show a renowned luxury Italian fashion brand wanted to customise the environment (flooring and walls) for a minimal surface area. Between the initial idea to approval of the panel samples for production it took one week. Handled between Milan and Bari, the former conceiving the digital image, the latter processing it and printing it. Regardless of quantities, the price per piece is virtually the same. Using another technique, such as rotary printing, this would have required a 30 to 60-day period and minimum quantities to cover the roller engraving costs. Using decorative paper, we would be more or less as quick, but decorative choices are limited and there is no chance for customisation. Either you produce large quantities to reduce unit costs or accept high costs and reduce the overall quantity. So why hesitate? Digital printing is faster, simpler and in line with market trends.
How to make the most of digital printing
Implementing a Print Quality System based on daily print quality assessments and maintenance is one way of ensuring the highest quality at all times. Managed by our proprietary software, parameters are verified on a daily basis, checking for missing nozzles, deviated nozzles and running test pattern prints to adjust alignment and ink deposit density. Corrections are made electronically, and the use of redundant colour bars helps avoid the need to stop production when one colour nozzle clogs up because the second one copes adequately.