
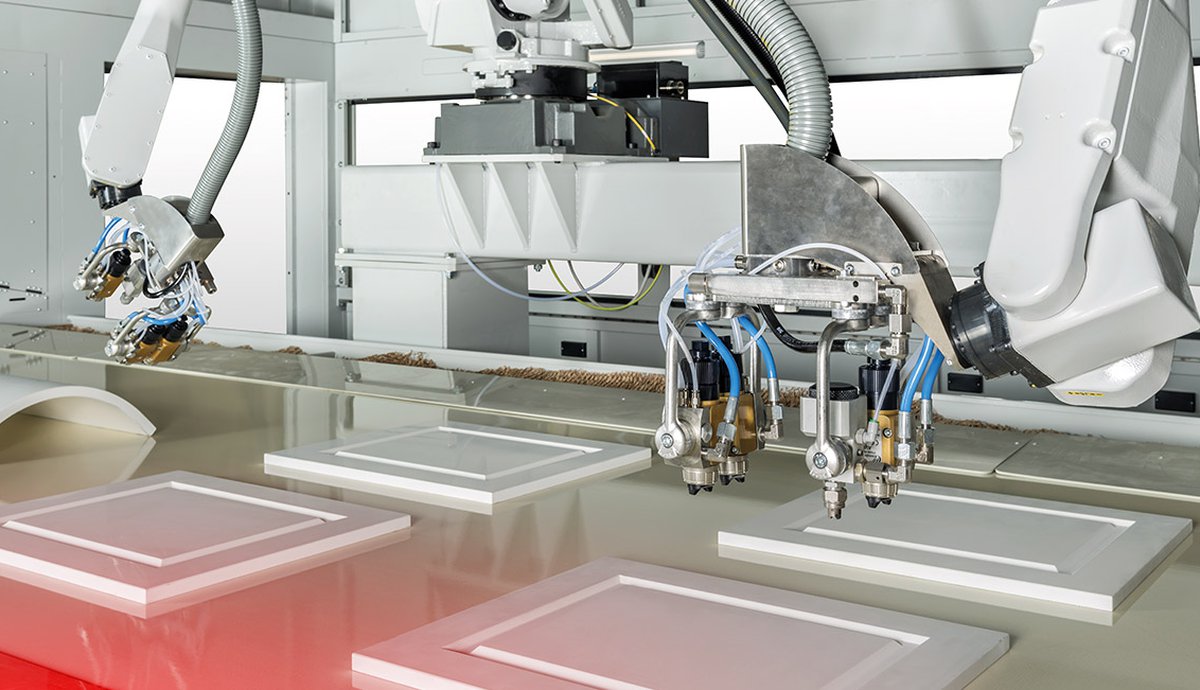
…is like the first time you used a dishwasher. Maybe not exactly, but think of it this way: put the dishes in, add the detergent, switch on and relax. You soon forget about piles of dirty dishes, running water, drying racks, soggy sponges, towels and wet hands.
Automated spray-coating equipment is efficient, consumes less lacquer and ensures consistent quality. The result you achieve first thing in the morning is the same as the quality obtained after 8 hours spent spraying panels. Because automated spray-coating machines don’t get tired or stop for coffee.
At Cefla Live we showcase a selection of automated spray-coating solutions all running to demonstrate the benefits of an affordable investment. Prima represents an upgrade which brings immediate savings in lacquer consumption. Perfect for businesses moving from manual to automatic spraying, this one-arm reciprocating spray machine will solve just-in-time requests and ensure fast returns on investment. Together with our partner IVM Chemicals srl, we will be coating panels which then run through our new excimer oven, Exydry-Z, to achieve a deep matt, fingerprint-proof, soft-touch finish.
Other spray-coating machines on show during the event include: Mito, entrusted to our partner ICRO COATINGS S.p.A. for live demos, Easy with Cefla Finishing partner Sirca S.p.A. and iBotic which will be in action using Sayerlack and Oece lacquers.
Featured on iBotic, participants will witness the new energy-saving system PowerBack, which retrieves energy from the machine’s decelerating spray arms in order to help power the outlet fan, saving at least 10% on energy costs compared to the iBotic without PowerBack.
More savings through our patented spray cleaning technology
Working with a sprayer or a robot with a belt for paint recovery means cleaning the belt regularly and the more paint you recover, the less you spend. If your spray cleaning system is conventional, you will not only throw away a lot of paint, but you will also use a significant amount of detergent. Conventional systems also lead to rapid belt deterioration, either through the abrasion from belt cleaner blades or aggressive solvents.
A system ensuring maximum cleaning potential recovers more paint and enables you to use less detergent during running time. Less detergent means lower operating costs, it safeguards your equipment and ensures a healthier environment. Our patented spray cleaning system ensures greater paint recovery, lower detergent consumption, fewer stoppages to replace belts, shorter cleaning times and, above all, enhanced production efficiency.