Past, present and future success for Estonia’s Haapsalu Uksetehas
Project Data
Customer:
Haapsalu Uksetehas
Country:
Estonia
Media Video:
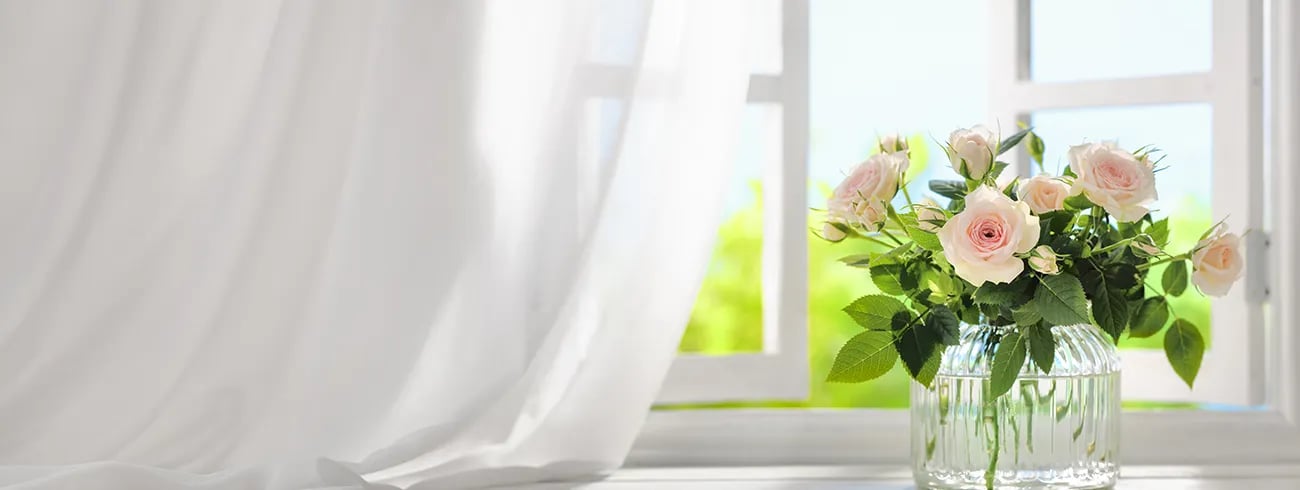
Haapsalu Uksetehas: Estonia’s first factory to use contemporary technology to manufacture interior and exterior doors
Founded in 1991, Haapsalu Uksetehas was the first factory in Estonia to use contemporary technology to manufacture interior and exterior doors for private and public buildings. In 1996, production of wooden and wood-aluminium turn-and-tilt windows started, but the focus is still on doors representing 90% of an annual turnover of 12 M euro. Daily operations are performed by 175 employees on more than 10 000 m² of production area. The products range from normal sandwich type interior doors with different core materials and way of finish to sound- and fire-rated technical doors for offices, schools, kindergartens, hospitals, hotels etc. Roughly 50% of products are exported to Finland, Norway and Sweden. The R&D department performs dozens of tests each year in order to ascertain the characteristics and performance of all products.
As there is no mass production in the factory, Haapsalu Uksetehas can assure customers of personal attention regarding the design and optional extras to make the most out of the product. Flexibility is the keyword and as the services provided include everything, starting from taking the measurements up to final installation, the company benefits from a true hands-on feeling regarding the entire process.
Production starts from the moulding of finger-jointed and laminated components made of pinewood. Manufacturing of stiles and rails as well as thresholds or glazing beads are all under control, thus enabling flexible and just-in-time production and quality. Less energy consumption, waste minimisation and green thinking have long been keywords for the company – boiler houses are run on chips from production, aspiration systems with heat exchangers save energy for heating and only water-based finishing materials are used in order to reduce the environmental impact. As a factory working with different projects, manual labour can´t always be avoided, but up-to-date technologies wherever possible and six CNC machining centres are helpful in this battle.
A recent investment was made to build a new production hall of 2600 m² with all the facilities for employees and supervisors. The so-called core investment was the new finishing line with stackers, turning device and sanding technology. The reason for that was a production security issue, because the existing finishing line from Cefla dated back to 2005, working in two shifts and occasionally even during the weekends, so if anything unexpected should happen, there was no plan B. In order to improve logistics and through-feed time, some other pieces of equipment such as an edge-bander, through-feed CNC drilling and milling machine and CNC working centre will be added in the near future.
The competition among the suppliers of finishing lines was really tough, but the choice landed on Cefla Finishing due to the staff’s in-depth attitude the many energy-saving extras available on the line, which have proved to be indispensable during the two-month test period.
“After 15 years with our old Cefla line, which has served us very well, we are convinced that the new line, which is full of improvements, will serve us in the same way for many years to come. Interfaces of the line are very operator-friendly and employees working on the old line get used to the new one in just a couple of days.” commented Rene Serg, the company’s R&D Manager, who went on to conclude: “Choosing a finishing line, especially for the very first time, is a complicated task, so you need a partner who really understands your needs and finishing materials. Cefla has patience and an in-depth attitude to answer a lot of “silly” questions and perform tests with your own materials in their LAB.”
Haapsalu Uksetehas has been a customer of Cefla Finishing for 15 years. Top-quality service and rapid response times to needs for spare parts are just other valid reasons for placing their trust in the Italian company.