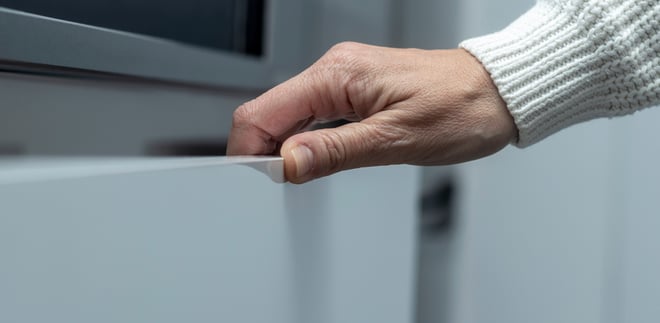
The advantages of vacuum primer application on panels
Any flat panel made of wood or wood-based materials, including those with rounded edges, can be coated using vacuum technology.
This makes it an ideal solution for manufacturers aiming for uniform finishes while minimising imperfections and achieving extremely smooth surfaces. The vacuum process takes place in a controlled environment, reducing the risk of dust contamination. This is the key to higher precision and longer-lasting products.
Compared to spray coating, vacuum coating also results in faster drying times, enabling quicker production cycles and reducing material waste. This innovation not only improves the aesthetic quality of panels, but also improves the operational efficiency of production processes.
The result? Perfectly finished surfaces with minimal material waste and much better final quality.
Smartvacuum: Cefla Finishing’s vacuum coating technology in detail
Given the advantages of vacuum technology, Cefla Finishing has developed a user-friendly solution for processing flat panels with rounded edges, J-Pull versions, and panels with ABS edges.
Smartvacuum is a machine capable of applying 100% UV acrylic lacquer in a single pass, without any physical contact between the application head and the substrate. Thanks to vacuum technology, it deposits between 90 and 140 g/m² of product with extreme precision and uniformity, avoiding build-ups on any part of the panel.
The flash-off phase takes place after primer application and before final drying in a UV-R oven.
The use of 100% solid UV products makes the process more sustainable, and the finish remains more stable over time compared to polyurethane or polyester-based products, also requiring shorter drying times.
A complementary solution to other application techniques
As mentioned, vacuum technology offers numerous advantages over other finishing methods, but this does not mean it should be seen as an exclusive alternative to existing solutions. To truly appreciate its benefits, companies should evaluate their traditional finishing lines and determine the best integration between existing machinery and vacuum technology.
Roller coating lines
Roller coating is one of the most widely used surface finishing techniques for flat panels. The process typically involves:
- Substrate sanding
- Primer application for adhesion
- Three layers of primer applied with single and double application rollers, with intermediate gelling
- Final drying
- Sanding of the primer coat, followed by finishing
Curtain coating lines
Curtain coating is performed using machines called curtain coaters. These systems utilise liquid coatings that form a curtain of lacquer that falls onto the moving panel in a uniform fashion, allowing even coating application. The steps typically include:
- Substrate sanding
- Primer application for adhesion
- UV gelling
- UV primer application using a curtain coater and flash-off tunnel
- Drying
- Sanding of the primer coat, followed by finishing
Spray coating lines
Spray coating lines use a closed-loop system for applying polyurethane or polyester-based primers in multiple layers on flat surfaces and edges. This set-up requires extended drying times, as panels must be stabilised at appropriate intervals before sanding and finishing.
Vacuum application technology: a comparative advantage
When correctly implemented alongside traditional techniques, vacuum technology enhances finishing processes, making them more efficient and sustainable.
The eco-friendly nature of 100% UV acrylic lacquers offers several advantages, reducing material consumption, costs, lead times, handling requirements and equipment footprint.
Additionally, when vacuum application is integrated with traditional methods:
- Rounded corners are obtained directly using vacuum coating technology, meaning you only need to sand the flat surfaces after drying
- Fewer machines required, meaning less cleaning and lower consumption
- Lower sanding costs and reduced material waste
- Shorter lead times and greater production flexibility
- Reduced machine footprint
- Fewer process stages, minimising handling needs
By implementing Cefla Finishing’s Smartvacuum, the finishing line would consist of the following steps:
- Panel sanding
- Primer application and gelling
- Application of 90-140 g/m² of 100% UV product in a single pass
- 2-5 minutes of flash-off
- Drying in UV lamp ovens
- Sanding and matt/gloss finishing as needed, using other known coating techniques
Smartvacuum: the perfect partner for Smartedge
Smartvacuum works best when paired with another Cefla Finishing solution: Smartedge, a machine for edge coating, filling and sanding, configurable with modular options to meet different quality and productivity needs.
The coating application can be performed with a traditional vertical roller, a patented soft vertical roller that automatically adapts to edge shapes without the need for counter-shapes, or using vacuum technology.
Smartedge and Smartvacuum share both technique and lacquer. This ensures optimal continuity between the flat surface and the panel edge.
The result? A smoother finish compared to conventional application techniques, especially on panels with rounded edges. This reduces the number of steps required to process semi-finished products and, most importantly, helps achieve a high-quality final product.
LOOKING FOR THE PERFECT FINISHING LINE SOLUTION?