Mixal doubles the efficiency of made-to-measure window manufacturing
PROJECT DETAILS
Customer:
Mixal
Country:
France
Media Video:
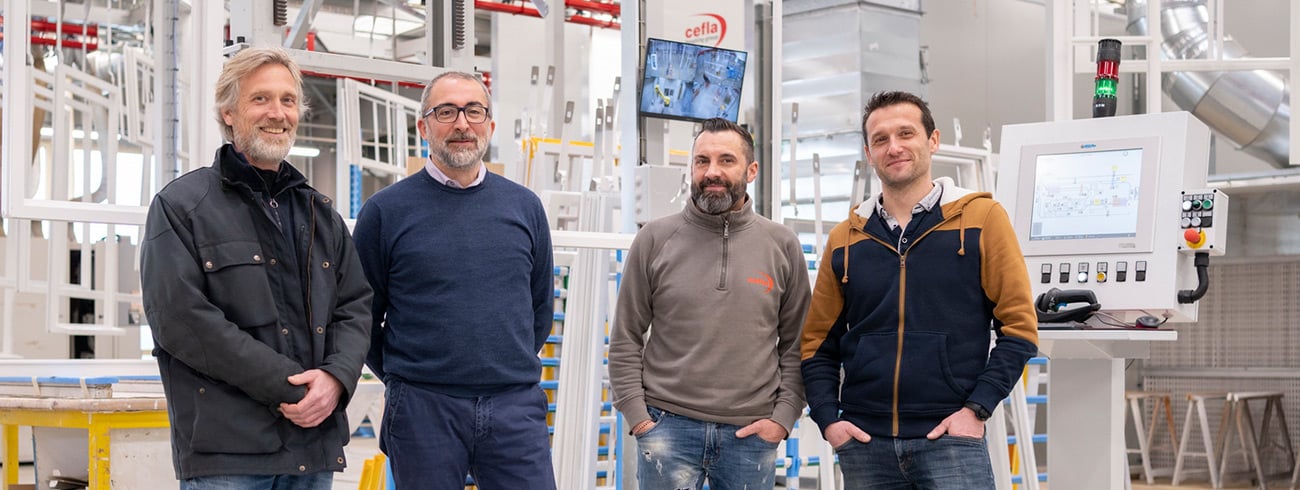
Who’s the customer?
Mixal, a French company belonging to the FPEE group, has 30 years of unmatched experience. It specialises in the production of custom-made window frames, both in wood and aluminium. For some years, however, it has focused exclusively on wooden frames, creating only custom-made windows of non-standard dimensions. The entire process, including the creation and application of colours, is performed in-house.
The challenge
Mixal set itself the dual goals of raising output capacity and increasing the efficiency of its custom manufacturing and finishing processes. But how best to boost productivity in a business where each window is made to measure? In order to increase output capacity and grow, Mixal has invested heavily in customised production and finishing processes that are increasingly fast and efficient.
The Cefla Finishing solution
The new ‘made in Cefla’ coating system has replaced the previous line, which involved frequent manual handling. The new system features the innovative iGiotto Mirror, a high-precision 6-axis coating robot. In combination with an automated conveyor system, the new robot can coat window frames continuously, without any interruptions to the process.
Results
The new finishing line allows for the manufacture of one-off pieces, drastically reducing, if not eliminating, downtimes and manual tasks. Investment in technology - the new Cefla plant included - has seen Mixal reduce its labour requirements by 50% and double productivity. Today, the company enjoys margins wide enough to continue offering high-quality, tailor-made window frames at competitive prices.
Mixal doubles the efficiency of made-to-measure window manufacturing
“On this project, Cefla offered the advantages of first-class support, extensive experience in designing lines and valuable advice during the plant set-up.”
Anthony Morin, Director of Mixal
To distinguish yourself on the market, you often have to make bold decisions. By focusing exclusively on the manufacture of personalised, non-standard frames, Mixal has demonstrated an ability to look beyond difficulties and seize the potential of customisation.
Mixal has invested for three years running in a major innovation project, allocating a total budget of €9 million. This project has achieved the twin goals of increasing output capacity and of maximizing efficiency and productivity.
Investment was channelled into two new areas: a new machining centre and a new Cefla coating line, which became operational in January 2023. Such investments were a major step for the company, and as such required rapid returns in terms of productivity in order to capitalise on them.
Custom-made products: at what price?
Offering a product of customised size and colour can be the key to success in the construction sector. That said, success can only be achieved when manufacturers have the technology needed to make tailor-made production economically viable.
So how is it possible to develop an efficient industrialised production process when making individual custom-made pieces?
The solutions proposed by Cefla focus on zero downtime, repeatable coating operations, flexible colour changeovers, automation and the application of industrial software capable of orchestrating an efficient mechanism that’s perfect down to the last detail. In the piece loading area, all the process information is brought together to ensure the line autonomously feeds the various coating and drying areas.
The new Mixal plant doubles productivity and reduces the number of manual tasks
The Cefla Finishing plant replaces a simpler plant which had an overhead chain conveyor; the latter required constant piece handling in order to perform various processes along the line. This modus operandi did, in fact, allow for the manufacture of one-off pieces, but at what cost?
The system had multiple disadvantages, such as interruptions to the coating process and, therefore, poor operational efficiency.
With the new plant, the handling system is fully automated. At the heart of the line lie the coating areas: one dedicated to flow coating and the other to spray-applied primers and finishes where the 6-axis anthropomorphic robot iGiotto Mirror works continuously, coating components as they’re fed gradually and automatically. The new line features:
- Overhead chain conveyor
- Preservative application and drying line
- In-line brushing zone
- Primer application-drying and spray finish line
- Masking zone
- Piece storage zone
The new line and Mixal's investment in technology has led to a significant drop in downtime and a considerable increase in productivity.
"Looking at the factory as a whole, investments have increased productivity by approximately 50%, both on the part of the new machining centre and on the finishing line, where labour requirements have been practically halved” stated Anthony Morin, Director of Mixal.
But that’s not all: there were other benefits.
Better safety, fewer risks for personnel
Mr. Morin pointed out that the company has also benefited enormously from a safety perspective. On the previous finishing line, in fact, workers had to replace the pieces to be coated by hand. Continuous manual handling of loads had a major impact on workers’ health, particularly as regards MSDs (musculoskeletal disorders).
“We’re no longer forced to continuously load and unload the line. For workers, that means no more load switching and, therefore, fewer MSDs”, commented the Director of Mixal.
The partnership with Cefla Finishing
The solid partnership between Mixal and Cefla Finishing has played a crucial role in the success of the new coating line. The relationship has gone from strength to strength thanks to close support from Cefla experts: skilled, reliable and on schedule, meeting the company's needs in terms of project consultancy and line construction.
“Once the specifications had been set and the project outlined, the new turnkey plant soon became a reality. Installation, staff training and the start of management all happened extremely fast”, said Anthony Morin.
As we know, prompt, high-quality assistance is crucial for companies looking to implement a new plant, as the potential of the new line needs to be exploited as soon as possible.
That’s why Cefla is meticulously attentive throughout every step of the partnership: from consultancy to design, from training to assistance. Customers are never left to fend for themselves. They receive a turnkey system: complete and fully operational, ready to go to meet company goals.
“I would have absolutely no hesitation in recommending Cefla, especially as regards the 'turnkey' aspects of the project and the excellent teamwork we enjoyed with them.”
Anthony Morin, Director of Mixal
Project Gallery
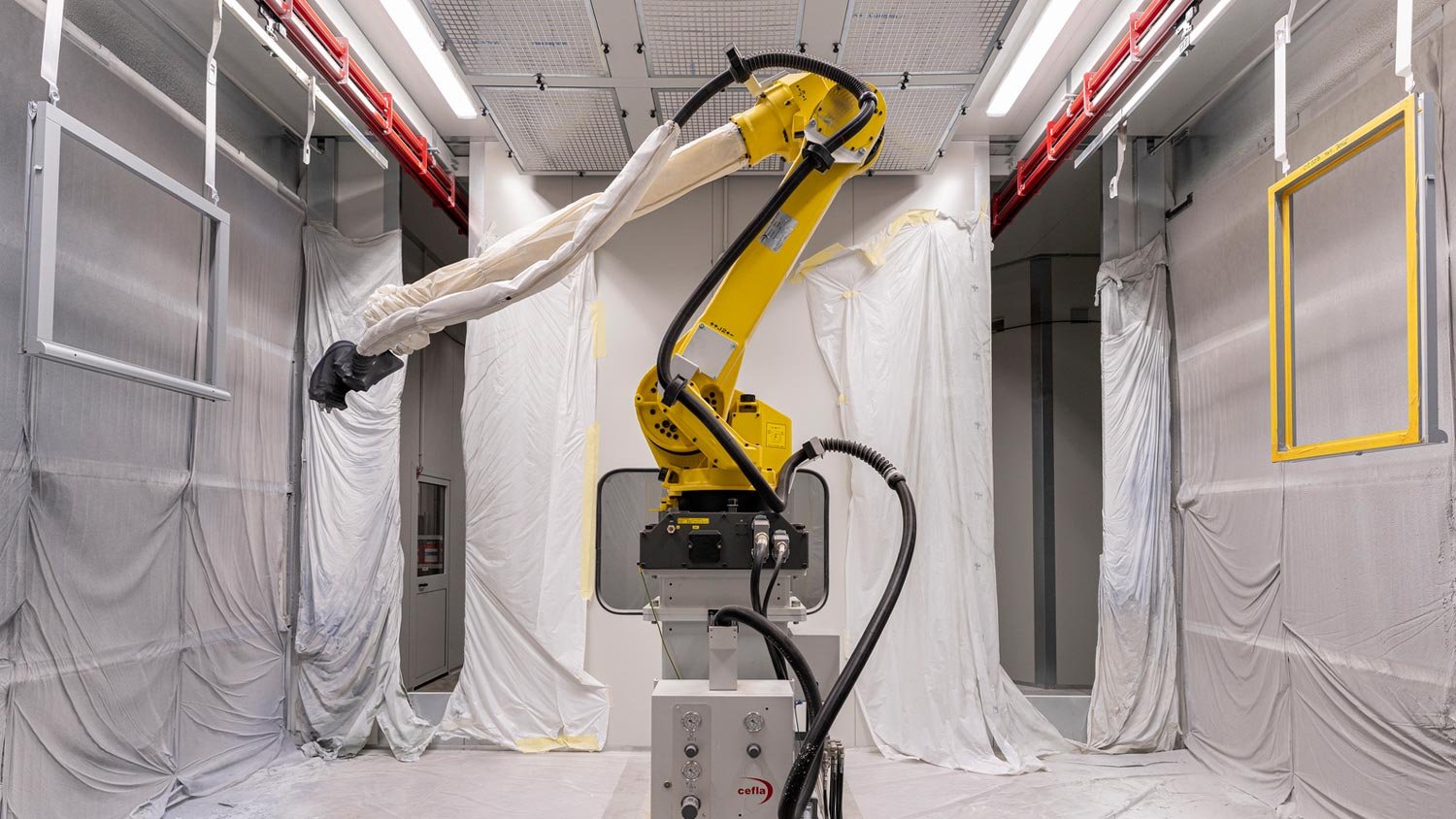
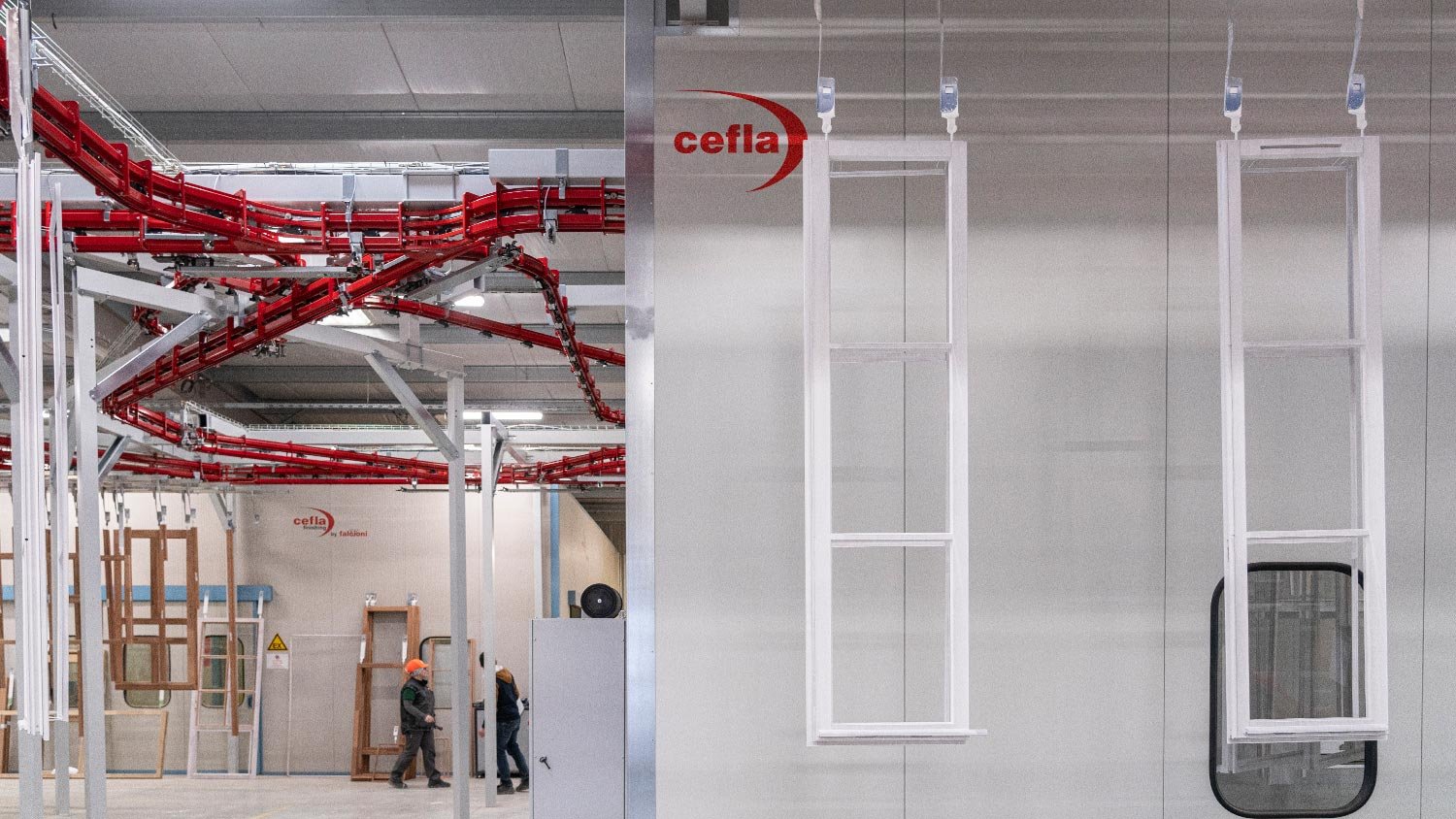
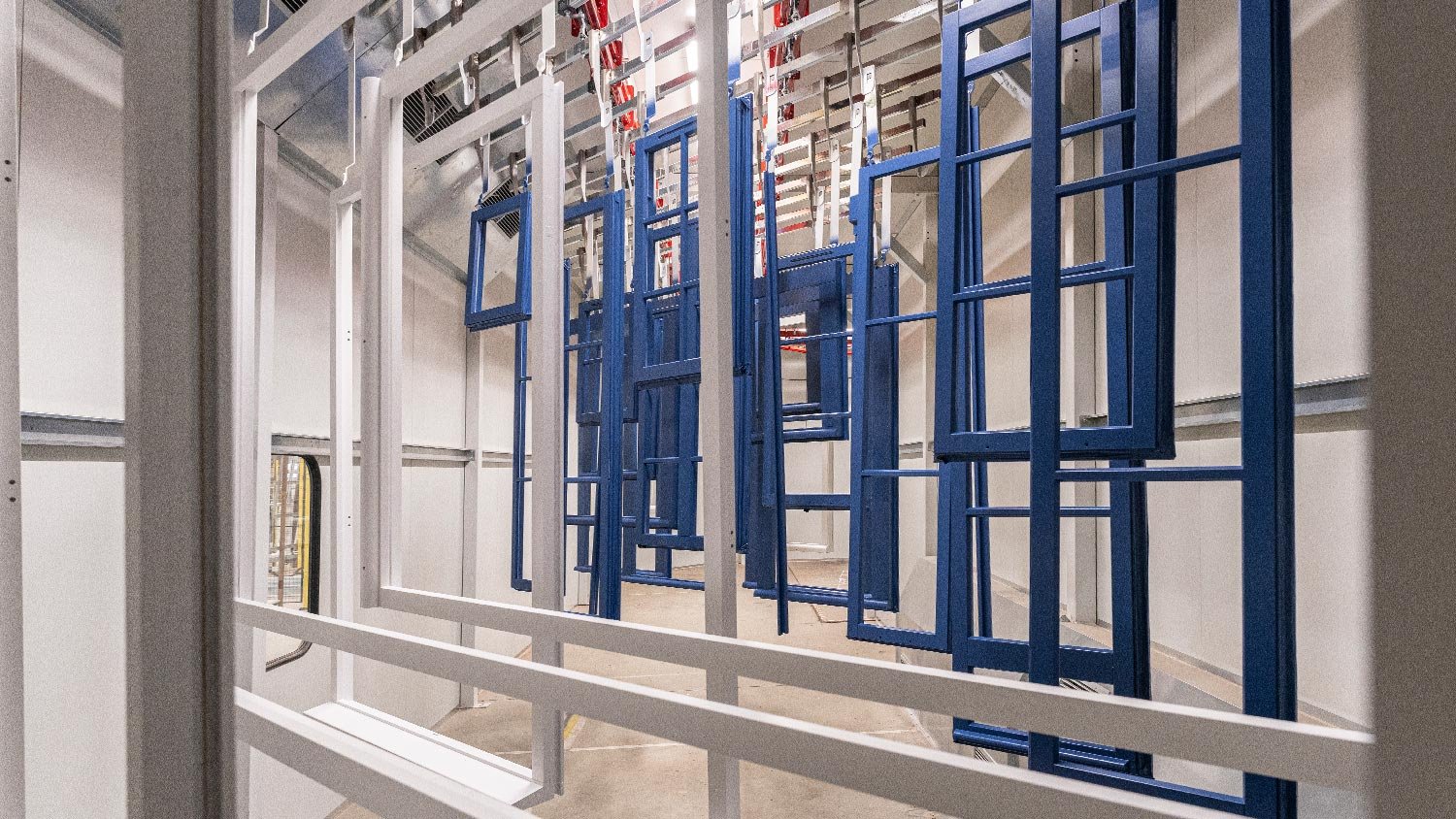